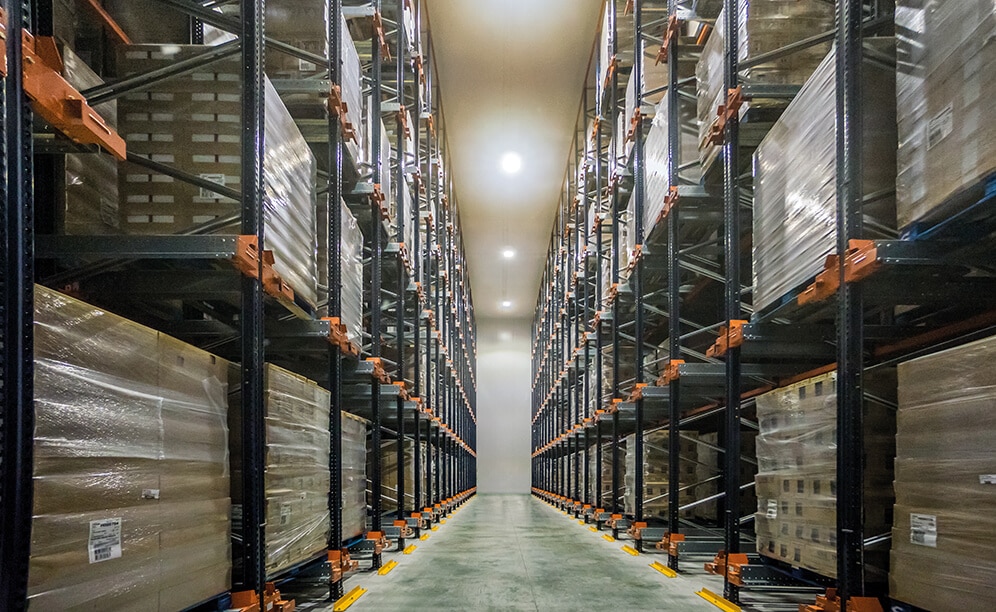
Six high-tech frozen storage chambers at Alfrisan
Drive-in pallet racks and the Pallet Shuttle system equipp the Alfrisan’s logistics centre
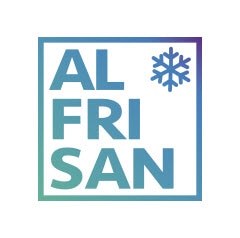
Alfrisan runs a logistics centre in the town of San Isidro (Spain) comprised of six freezer chambers. Mecalux equipped three chambers with the Pallet Shuttle system and another three with drive-in pallet racks. Both solutions provide the best storage capacity to meet the warehouse fulfilment processes of the company.
About Alfrisan
Almacenes Frigoríficos San Isidro (Alfrisan) is a logistics operator specialising in controlled temperature products. It was founded by José Francisco Antón Ruiz in 2016, who has extensive experience in the sector. He also owns the more than a decade old, frozen wholesale storage company, Alguazas Fish.
The logistics centre
The company owns and operates a logistics centre in the town of San Isidro, in the province of Alicante (Spain). Comprised of six different chambers, this streamlines the organisation of the goods depending on their level of demand.
Mecalux has equipped the frozen storage chambers with two different storage systems: drive-in pallet racks and the Pallet Shuttle system that, overall, has a storage capacity of 8,920 pallets.
- Chamber 1. Pallet Shuttle system with FIFO (first in, first out) management.
- Chambers 2 & 3. Pallet Shuttle system with LIFO (last in, first out) management.
- Chambers 4, 5 & 6. Drive-in pallet racking.
Chamber using the Pallet Shuttle system
This high-density storage system fully uses the available space to provide greater storage capacity. The racks are 14.5 m high and are allocated to the low demand products.
Operations are very fast and straightforward, and require minimal labour: operators place the motorised shuttle into the corresponding channel, deposit the pallets in the first position of the racks and the Pallet Shuttle transfers them directly to the next free location autonomously. When removing the goods, the same process takes place but in reverse order.
In one of the frozen storage chambers, the load is managed via the FIFO method, i.e., the first pallet to enter is the first to leave. There are dual work aisles, one for entries and another for exits, and the block of racks runs down the centre of them. By having two aisles, there is no interference between the forklifts that load the pallets and those that unload them.
The rest of the frozen storage installations using the Pallet Shuttle system fulfils the LIFO criteria (the last pallet to enter is the first to leave). An aisle was enabled in the middle of the two blocks of racks, so pallets enter and leave on the same side.
Control tablet
The installation is equipped with tablets used to send orders to the Pallet Shuttles. They have a tactile interface and a very intuitive software that fosters the interaction with all the shuttles in the logistics centre, always fulfilling the established protocol.
The tablets run a very diverse set of functions:
- Selection of the shuttles in operation and verification of their status.
- Choice of pallets it will operate with.
- Continuous loading and unloading of channels.
- Inventory check to count the number of pallets stored automatically.
- Management of users and authorised personnel.
- Location of the shuttles through an audible, lit signal.
The shuttles incorporate cameras and use tablets as monitors to reproduce images. Thus, the operator visualises the direction and movement of the forks when introducing the Pallet Shuttle into the channel and can position it correctly.
Battery charging
A compartment is set up outside the frozen storage area to carry out battery charging.
Batteries extracted from the shuttles are connected by simply fitting them into the charging stations. There is also a separate cable that connects directly to the shuttle, without needing to remove the battery.
The logistics centre has reserve batteries to prevent stops in shuttle operations. One can load a piece of equipment, while the Pallet Shuttle continues to operate in the assigned channels.
Drive-in pallet racking
Mecalux has installed drive-in pallet racks for the high-demand products in three frozen storage chambers. Each of these contains a central aisle and two very deep, 5 m high blocks of racks on both sides.
The racks comprise a set of 13 m high lanes, with five levels equipped with support rails and pallet centralisers for proper insertion of the loads.
The pallet trucks enter the inner lanes with the load raised above the level it will be deposited. Both loading and unloading of the goods are performed in the same aisle, but in reverse order.
Guide rails are installed on both sides of the floor, so the machinery runs centrally, simplifying pallet truck manoeuvres and preventing blows against the rack structure.
Likewise, as a safety measure, the outer portion of the uprights is protected with vertical reinforcement to minimise possible bashes from the forklifts.
Advantages for Alfrisan
- Optimal organisation: the inclusion of drive-in racks and the Pallet Shuttle system aids in proper load management and sorting according to the level of demand.
- Maximum storage capacity: the Alfrisan logistics centre can house 8,920 pallets.
- Safety guaranteed: the available storage solutions contain safety devices for maximum protection of the structure, the goods and the personnel.
Pallet Shuttle system | |
---|---|
Storage capacity chamber 1: | 1,785 pallets |
Storage capacity chamber 2: | 2,100 pallets |
Storage capacity chamber 3: | 1,615 pallets |
Pallet size: | 800 x 1,200 mm |
Racking height: | 14.5 m |
Gallery
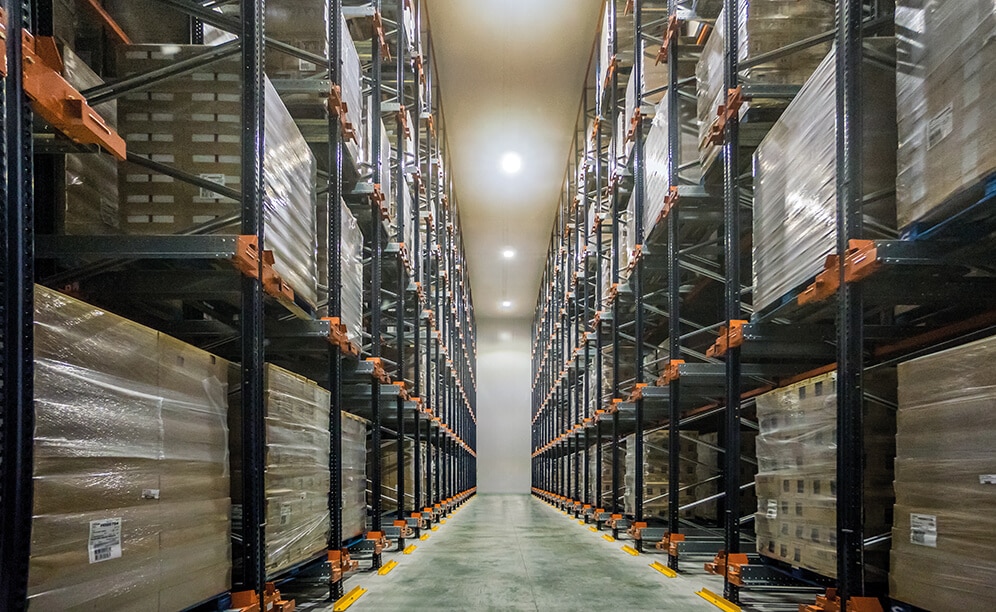
Mecalux ha equipado las cámaras con dos sistemas de almacenaje diferentes: paletización compacta drive-in y Pallet Shuttle
Ask an expert