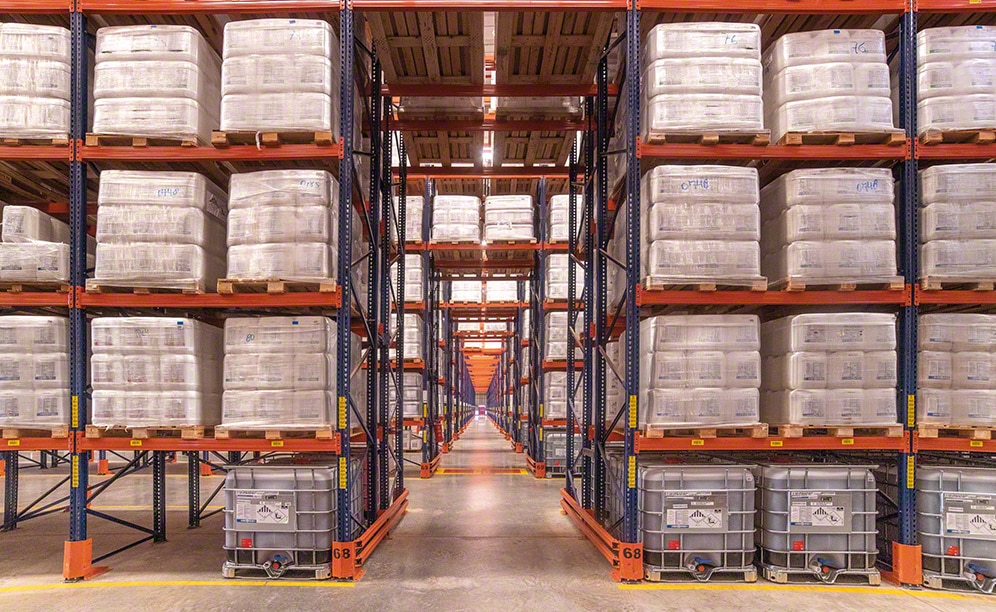
Eight argochemical product warehouses of Bravo in Brazil
Direct access to manage the agrochemical products of Bravo
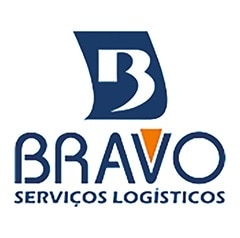
Union means strength. The agrochemical logistics operator Bravo had the backing of Mecalux when it came to equipping its new warehouse in the town of Cuiabá (Brazil). To this effect, there are already eight Bravo logistics centres with Mecalux storage solutions. Pallet racks were the chosen rack in all of them because they facilitate the management of colossal pallet flow volumes that happen each day.
Vicinity and growth
Bravo is a logistics operator who specialises in the storage and distribution of agrochemicals. In other words, chemical substances used to repeal, kill, attract, regulate or stop the growth or spread of pests on farmland.
Bravo has long-standing experience managing this type of product (it works for brands like Syngenta, Bayer, Arysta, Rotam, FMC, UPL, DOW or DuPont, among others). According to Elimar Elesbon Soares, the company’s operations director, “we listened closely to our customers’ needs and set up shop as close as was feasibly possible to them to streamline deliveries and be more competitive.”
In the fields, farmers monitor all phases of crop growth very closely. In each one of these stages, they need specific products that ensure agricultural development of food crops. “When it is time to spray a certain pesticide, this product’s demand goes through the roof very briefly, which reduces our response times dramatically,” explains Bravo’s operations director. “That is why our strategy is to set up our warehouses close to the country’s main agricultural areas and to make deliveries to customers on the double.”
Bravo has flourished from its beginnings. “Our business vision has driven our expansion and because customers have asked us to be close by,” points out Elimar Elesbon Soares. “In all our warehouse, we knew very clearly that we had to reduce operational overhead and trim delivery times,” he adds.
Overall, the company owns and operates fourteen warehouses spread all over Brazilian territory. Eight of these are equipped with pallet racks from Mecalux. “We trust Mecalux because of it logistics know-how and because it is a global leader in the sector. Its product quality leads the pack. Mecalux is a partner which, in all our projects, has really understood our business needs and how urgent it was to get racks up and running.”
Daily, the warehouse receives goods from customer production plants and, later, distributes them to cultivated fields. Some of these pallets are also sent to rural or agricultural goods shops. “Between February and August, we receive more inflowing products. In contrast, January is when we distribute the most,” adds Elimar Elesbon Soares.
Practicality made pallet racks the right choice for all the warehouses. According to Elimar Elesbon Soares, “At 12 m high, we make the most of our warehouse space. Plus, we organise products according to their demand and manage everything through the FIFO criterion (first in, first out).” Sound organisation of goods and all these operations are essential to facilitate incoming and outgoing pesticides.
Agrochemicals: handle with care
Pesticides utilised to wipe out infestations are either poisonous to people and water, or the environment. Thus, they must be stored and handled in a completely safe manner to avoid potential risks.
According to the UN Food and Agriculture Organisation, the following are some of the issues companies like Bravo must pay special attention to in their logistics centres:
- Location. Pesticide warehouses must be far from households, hospitals, schools, shops, food markets, rivers, wells and other domestic water sources.
- Accessibility. These warehouses must be easily accessible to vehicles moving pesticides, as well as fire-fighting equipment and vehicles (if a fire-related incident occurs).
- Limit handling. Any distribution warehouse racks must facilitate minimum product handling to avoid spills and leaks.
- Lighting and ventilation. Lighting work zones is necessary (natural and electric), with wide spaces for handling loads.
- Space allotted to personnel. Installations must be set up with washing facilities for personnel.
- Structure. Walls must be smooth, uncracked and ledge-free, electrical connections must be insulated with fire- and dust-resistant materials, and warehouse sectors must be separated by firewalls.
- Fire-protection systems. The warehouse must have smoke detectors and control devices that react directly above the area affected by a fire outbreak. Automatic sprinkler systems should be distributed strategically inside the racks.
A fully space-purposed warehouse
“The majority of industries in this sector are located in the Southeast region of Brazil,” explains Elimar Elesbon Soares. So, recently, the company opened a brand new 35,000 m2 warehouse in the city of Cuiabá, in the State of Mato Grosso, “to reduce delivery times.”
Just like the other logistics installations in Brazil, Mecalux and Bravo work hand in hand in this project’s design. As Elimar Elesbon Soares explains, “Mecalux’s technical team visited our centre in the middle of its construction, and showed us which would be the best solutions to make full use of space and reach the storage capacity we wanted.”
In this warehouse, huge flows of goods are carried out every day. The centre has 36 docks with hydraulic ramps where 120 lorries load and unload daily (each with an average 27-pallet capacity). Every day, 3,300 pallets are managed (both inputs and outputs), “or in other words, an average of 2,200 tonnes of pesticide,” points out the operations director.
Pallet racks are ideal for handling this work volume. Among all their advantages, Elimar Elesbon Soares highlights “their handiness.” The racks provide direct access, which facilitates the handling of products. Using reach trucks, operators only must go to the specified location to insert and extract the pallets.
The distribution of the goods in the racks takes their features and sizes into account. Pallets are 1,000 x 1,200 mm, although they can be of different weights (from 1,050 kg, up to a maximum of 1,350 kg). For example, lower rack levels are allocated to IBC Pallet Tanks (bulk liquid containers), to prevent the accidental fall of these heavy, dangerous loads. Upper levels are where light-weight products are deposited.
When dealing with such long aisles (measuring 84 m long), the higher rotation products are placed at the ends with the intention of speeding up the inputs and outputs of these fast movers. Those with a lower rotation are set back further. Additionally, the racks were fitted out with two underpasses that cut across the racks to streamline workflows and, at the same time, to serve as emergency exits.
The Bravo operations director also emphasized “the flexibility of the racks, which let us adapt to our changing customer base and market trends quickly.”
Elimar Elesbon Soares - Bravo’s Operational Director
“All the projects we have undertaken with Mecalux have been crucial to our company. Plus, we have a soft spot for our warehouse in Cuiabá because this location let us strengthen growth in Brazil. The Mecalux storage system makes full use of the entire surface area (racks stand up to an impressive eight levels high), which is how we got a larger storage capacity.”
Advantages for Bravo
- Safety first: the work at Bravo consists of managing agrochemical products in a completely safe manner. To do so, all it warehouses have a fire safety system that fulfils protection regulations.
- Business expansion: from its founding, Bravo has grown and taken its products closer to its customers. Mecalux has always collaborated with the company, offering up solutions that would reduce operational costs and minimise order delivery times.
- Higher productivity: all these warehouses are equipped with pallet racks because of their easy-to-use practicality, facilitating massive pesticide inputs and outputs.
Bravo warehouses with Mecalux racks | |
---|---|
Total built surface area: | 412,000 m² |
Total storage capacity: | 252,595 pallets |
Pallet size: | 1,000 x 1,200 mm |
Max. pallet weight: | 1,350 kg |
Racking height:: | 12 m |
Gallery
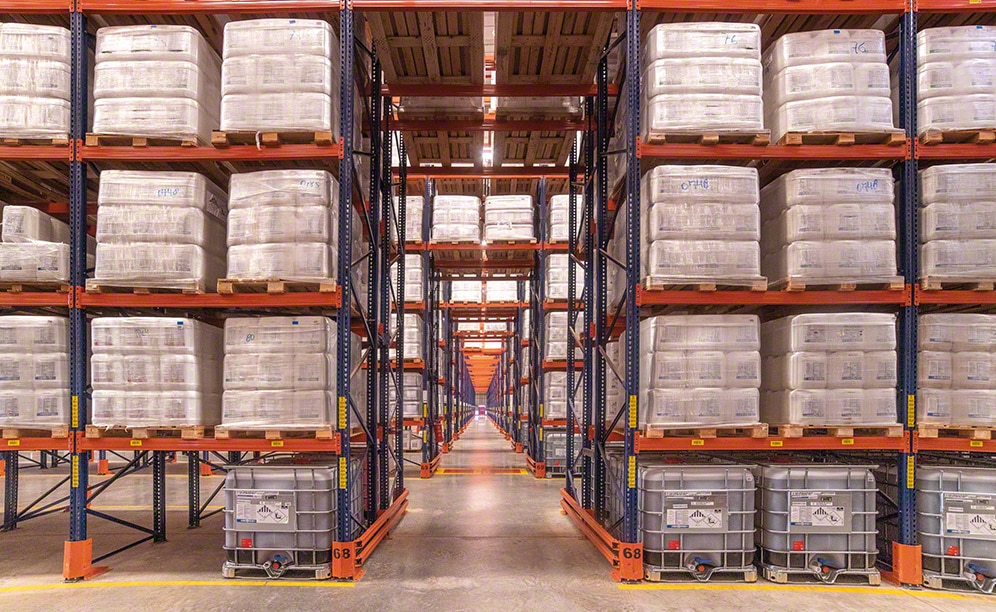
Pallet racks for Bravo's argochemical products
Ask an expert