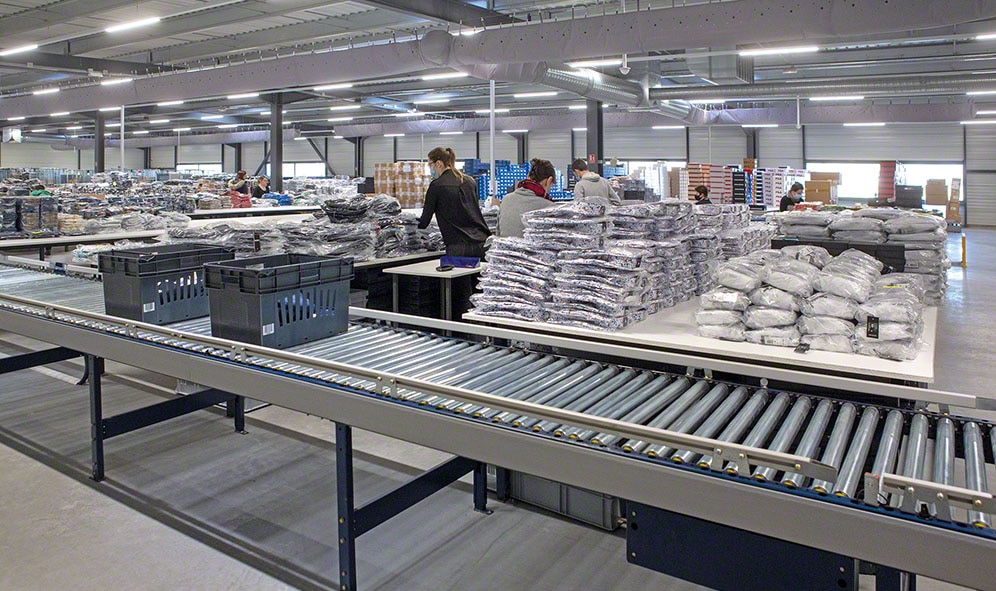
CCV: automatic conveyors for managing 20,000 products a day
CCV has increased the number of products it receives every day by 66%, up from 12,000 to 20,000

CCV has opened a new warehouse in north-east France designed to address its growth prospects and the challenges posed by omnichannel retail. To achieve this, Mecalux has installed a conveyor system for boxes aimed at increasing internal goods flows. The advantages? The number of products that this fashion retailer receives every day has risen by 66% compared to its previous installation, up from 12,000 to 20,000 products.
Growth and transformation
Founded in 1985 in Épinal, France, CCV is a multi-brand fashion retailer that sells prêt-à-porter items for men, women and children. Its slogan could not be more representative: “Ça change la vie” (in English, “It's life-changing”). CCV is characterised by continuous change and transformation with a view to expanding its market and serving a growing number of customers throughout France.
It currently boasts more than 30 shops all over the country with approximately 20,000 items of clothing and footwear from more than 150 well-known brands.
Following the success that came with the opening of its bricks-and-mortar shops, its next goal is to increase its online sales, which currently account for 5% of its total turnover. CCV aims to increase this share to 15% and to put in place an omnichannel business model.
Omnichannel is a marketing strategy especially beneficial for customers, as they have the option to choose between multiple channels when buying and receiving merchandise. For example, they can go to any of CCV’s 30 shops or, if they prefer, they can buy their products via the webpage and receive them at home, at a collection point or at any of the company’s bricks-and-mortar shops.
Nevertheless, omnichannel retail is highly complex from a logistics point of view. On the one hand, it requires a large space for accommodating all the products. On the other hand, it is crucial that operations be organised to a T so as to facilitate picking and dispatch orders in the shortest time possible.
Determined to implement an omnichannel strategy in its business, CCV has opened new 5,000 m² logistics installations in Capavenir-Vosges, just 10 km from Épinal. In addition to an administrative area, it has set up a 4,000 m² zone where it stores 100,000 products (approximately 12,000 SKUs) and receives 20,000 items per day.
More agility in the new facility
By commissioning this warehouse, it was very clear to CEO Michel Gladstein that CCV had to completely revamp its logistics systems. He explains, “Before, all our operations were manual. Operators had to make many trips when moving goods from one place to another, which took up a lot of time and increased the possibility of error.”
The company was fully aware that this was an aspect to improve upon: “Our priority was to shorten the distances that operators travelled because, with the time gained, they could concentrate on other tasks that would have an effect on the productivity of the entire facility. We also wanted to be able to increase the amount of product we moved every day while using the same number of employees,” says Gladstein.
To make operations more agile, the firm decided to implement a just-in-time working method, consisting of minimising the time taken to store and dispatch goods. The warehouse has on hand only the goods it needs to serve CCV’s customers, so many orders are prepared by means of cross-docking (as goods sent by suppliers arrive, they are directly distributed without having to be stored).
So, how was CCV able to streamline internal goods flows? After analysing the company’s needs, Mecalux came up with a full box conveyor system. Michel Gladstein indicates, “The conveyors operate very smoothly and are extremely practical. By cutting down on operator travel, these workers can concentrate on other manual tasks; this, we’ve eliminated downtime.”
The result has been a complete success. Now, CCV receives 20,000 products a day (that is, 66% more compared to the 12,000 it received at its old warehouse). Moreover, up to 800 orders are prepared and dispatched on a daily basis.
Automatic connection of different zones
The conveyors installed in the CCV facility automatically link the picking area with the goods consolidation and dispatch zone.
The operators working at the pick stations receive the palletised merchandise, mainly garments and footwear. Then, they begin to prepare the orders at large tables set up for this purpose. When the order is finished, they place the box on one of the two conveyor lines, assigned according to the pick station.
Spanning 34.5 m long, both lines automatically connect to a recirculation area. This zone is equipped with an automatic identification station with an RFID reader. When the box goes through this station, the system assigns it to one of five exit ramps. These 12 m long ramps are gravity-fed, that is, they have a slight incline to allow the boxes to move to the end of the conveyor independently. As each ramp can accumulate up to 19 boxes, a total of 95 can be stored awaiting dispatch.
The recirculation area serves to distribute the boxes in sequence on each ramp, hence, facilitating the subsequent consolidation and dispatch of the goods. In the event that one of the ramps is full of boxes, the system directs the box or boxes destined for that ramp to remain on the recirculation line until the ramp has been emptied.
“The conveyor has integrated perfectly with the organisation of our warehouse, and our operators have adapted easily to this new working tool,” enthuses the CEO. As an additional safety measure, the conveyor system has six pedestrian walkways in case, in an emergency, an operator needs to walk across the line.
Challenges of fashion logistics
Multi-brand retailer CCV has set for itself an ambitious objective: to serve a growing number of customers in its 30 shops throughout France and, at the same time, deliver orders to those who shop via its website (ccvmode.com).
How will it be able to do this? By streamlining operations at its warehouse in Capavenir-Vosges and facilitating the work of its staff by automating internal transport. This will ensure that operators can dedicate their time solely to preparing orders.
According to CCV CEO Michel Gladstein, “After comparing various proposals, we decided to go with Mecalux; it’s a leading company in the market, and that reaffirmed our decision. We’re more than satisfied with the result; Mecalux has shown us that it has the means of production to adapt to any need. On top of that, the monitoring carried out during the entire assembly process was extremely thorough.”
Mecalux’s conveyors help to do away with manual transfers of goods and, therefore, intensify the internal product flow. Thanks to automation, CCV’s new logistics centre is capable of storing 12,000 SKUs and managing the receipt of 20,000 products a day.
By using conveyors, we’ve ramped up our productivity: our processes are much quicker and more reliable. Right now, we’re maximising our online sales and, to do this, we need our order prep processes to be efficient. Thanks to the success of the conveyors, we just might consider automating more operations in our facility.
Advantages for CCV
- Increased throughput: with this new facility, the number of products CCV manages every day has risen by 66%.
- Speed and safety: the conveyors greatly expedite goods movements while minimising the risk of accidents. Moreover, operators can focus on other, more value-adding operations.
- Automatic connection: the conveyors automatically link the pick stations with the dispatch area and move orders safely and in sequence.
Gallery
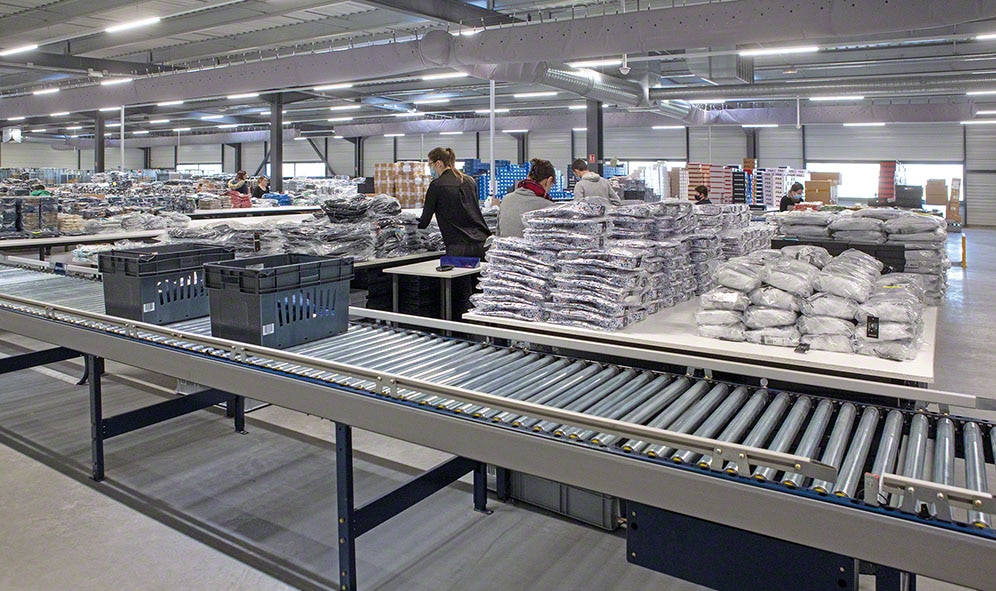
CCV stores 12,000 SKUs and manages 20,000 products a day
Ask an expert