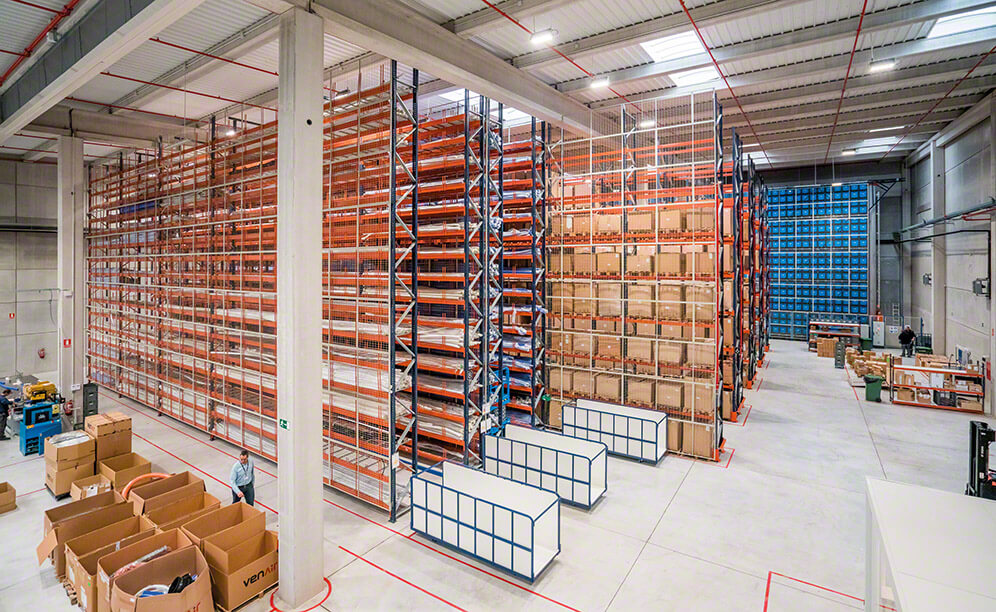
Triple storage solution: the Venair distribution centre
Venair combines pallet racks and an automated miniload warehouse
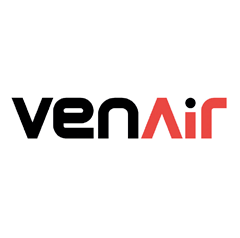
The Venair warehouse, a silicone hose manufacturing business, is equipped with three different storage systems by Mecalux: pallet racking, narrow aisle racking and an automated miniload system. The combination of these solutions maximises storage capacity and increases productivity, by classifying the products according to their size and turnover.
About Venair
Established near Barcelona in 1986, in the city of Terrassa, Venair is a family run business who designs and manufactures hoses and specialised silicone parts for distinct industries such as the pharmaceutical, biotech and aerospace sectors.
Its commitment to innovative production processes has earned Venair a place among the top five silicone hose manufacturers in the world, selling its products in more than 65 countries.
Three storage systems
Reorganising its warehouse’s distribution was what the company needed to do to deposit a broad range of different SKUs and sort them according to their demand level and dimensions.
Venair called on Mecalux to show the company in how to deal with growing business demands. The result is a warehouse where three different storage systems work side by side:
- High-rise racks with narrow aisles
- Pallet racking
- Automated miniload warehouse
Racks with narrow aisles
Two 1.1 m wide aisles were installed with pallet racking on both sides. These racks are arranged to store hoses and very long profiles.
The 11 m high racks make full use of the surface area and height of the warehouse in order to increment the storage capacity. Likewise, they include parts and accessories that make them ideal for products of various sizes and volumes.
The shelves are made of electro-welded mesh and, in addition, contain stops on the ends of all levels that prevent stored hoses from falling.
To reach the goods, the utilised lift machine is set up with a platform where the operator stands. From here, goods are inserted and extracted from their locations.
Miniload warehouse
It is composed of a single aisle with double-depth racks running down both sides, measuring 34 m long and 8 m high. This is where smaller-sized and low turnover products are housed.
A twin-mast stacker crane for boxes circulates in the aisles, whose task is to carry out the inputs and outputs of the goods automatically.
This machine operates at a travel velocity of 180 m/min and 100 m/min when hoisted, the best way to achieve the workflows Venair demands.
The miniload installation includes a telescopic fork extraction system that can access the second position in each racking location.
To transport boxes, the fork are inserted underneath the boxes.
A U-shaped picking station is installed on the side of the warehouse. Order prep fulfils the “product-to-person” principle, in other words, operators receive boxes flowing from the automatic warehouse. Next, they collect the articles the warehouse management system instructs them to and deposits them in one of the containers placed on a rack located behind them. Each container corresponds to an order.
A maintenance area is enabled at the rear of the warehouse, and sectioned off with safety doors.
The construction of the miniload warehouse takes Venair’s growth into account, consequently a space is readied to accommodate more boxes as needed.
Pallet racking
Mecalux has supplied 8.5 m high pallet racks and these provide a storage capacity for 2,072 pallets with a 600 kg unit weight.
These racks are noted for their versatility to adapt to a wide variety of SKUs of distinct sizes, turnovers and volumes. These house both palletised products and very long, wrapped hoses placed on a pallet.
Having direct access to the pallets is vital, since this provides high speeds when managing goods.
These racks are operated by reach trucks, able to work in a 3 m wide aisle and access the highest load levels.
Along the entire rear of the racks, facing the assembly and dispatch area, a protective mesh is placed to prevent the accidental fall of goods.
Dispatch and assembly area
One one side of the warehouse a wide area is set up for assembly and dispatch tasks. Here, hose is cut to length and products are readied for each order.
Right next to this, pallets from the same order or route are grouped on the warehouse’s floor, meant to streamline the loading of distribution lorries.
Easy WMS and Galileo
The automated miniload warehouse is managed by the Easy WMS warehouse management system by Mecalux, which is responsible for controlling and coordinating its correct operation. This system controls the various warehouse activities, which include the assigning of locations and the storage of boxes according to turnover, the extraction of goods and the preparation of orders.
Easy WMS by Mecalux is in constant two-way communication with Venair's general warehouse WMS and ERP, transferring data and information for maximum picking productivity.
By the same token, the Galileo control module sends motion commands to the stacker cranes and the automatic conveyors of the picking stations, guaranteeing safe operations.
Advantages for Venair
- Maximum storage capacity: the three storage systems deliver the storage capacity the company really needs.
- Productive management: the merchandise is distributed in the warehouse bearing in mind their characteristics and demand. Overall, this simplifies storage tasks and confers better installation throughput.
- Boosted picking speeds: the automated miniload warehouse and the picking station optimise the movements of the operators during picking.
Venair distribution centre: Pallet racking | |
---|---|
Storage capacity: | 2,072 pallets |
Pallet size: | 800 x 1,200 mm |
Max. pallet weight: | 600 kg |
Racking height: | 8.5 m |
Gallery
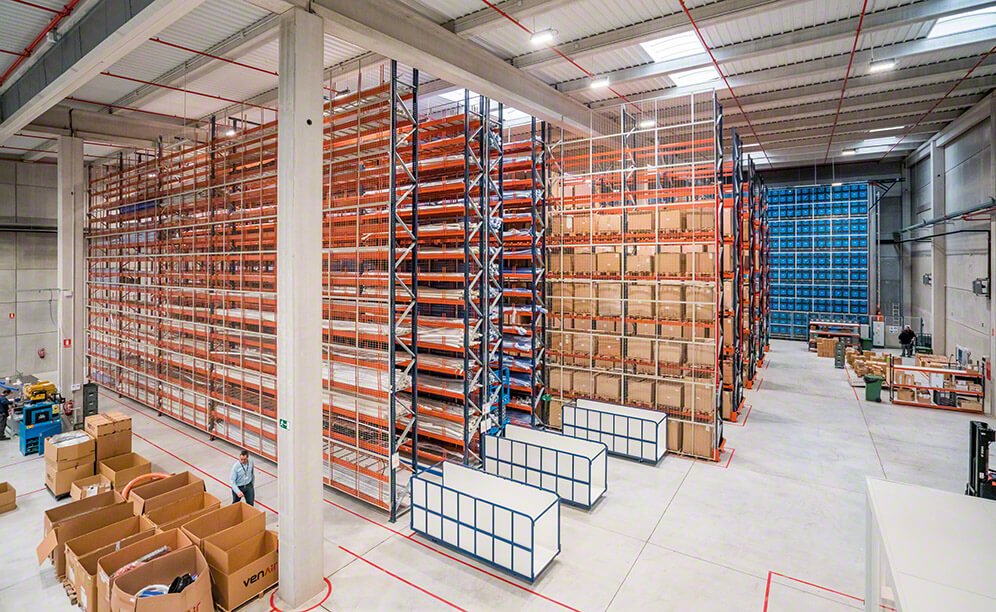
The Venair warehouse is equipped with three different storage systems by Mecalux: pallet racking, narrow aisle racking and an automated miniload system
Ask an expert