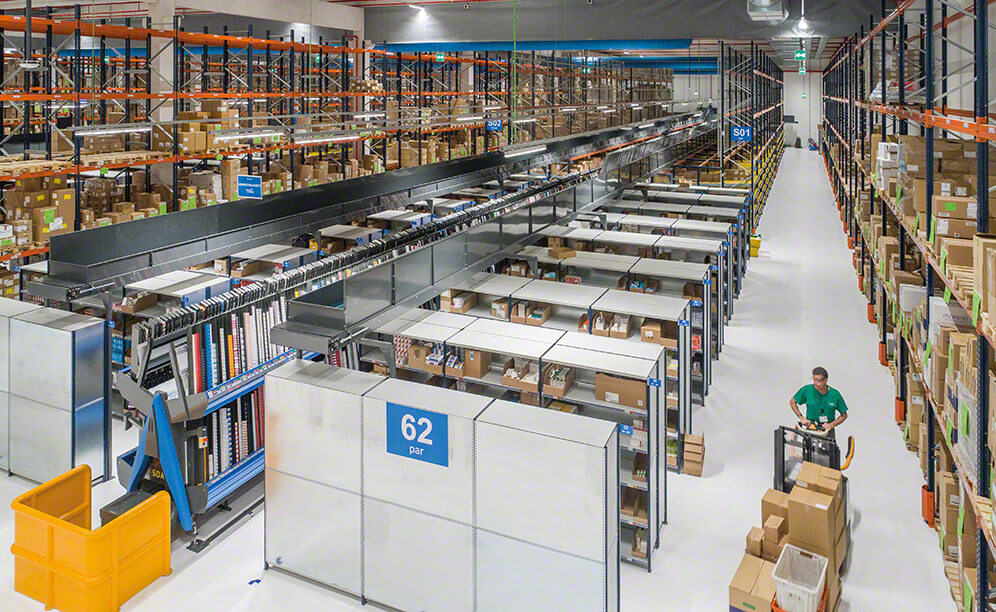
The logistics centre of the Alliance Healthcare wholesale pharmaceutical company in Lisbon was sectored into five zones to organise products according to demand
Storage for picking and automatic conveyors raise the throughput of Alliance Healthcare
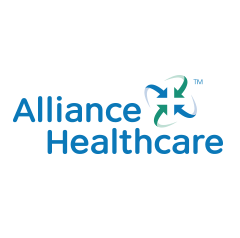
The logistics centre of Alliance Healthcare in Lisbon (Portugal) is dedicated to picking. Mecalux has provided all the storage equipment that makes up the installation: light-duty shelves, live storage for picking and pallet racks for reserve palletised goods. A conveyor circuit links the different areas of the centre and moves prepared orders to the consolidation and dispatch area.
Pharmaceutical industry supplier
Alliance Healthcare Portugal is an association between the Walgreens Boots Alliance (49%), the National Association of Pharmacies (49%) and José de Mello Participações II, SGPS (2%).
Specialised in wholesale pharmaceutical distribution, this company has a huge presence in the European market.
As the leading pharmaceutical distributor in Portugal, it employs close to 460 people and has warehouses in Alverca, Porto, Almancil and Castelo Branco. Its mission is to distribute medicine and sanitary products to more than 2,000 pharmacies spread throughout the country.
The logistics centre
The company needed to achieve maximum storage capacity in its logistics centre located in Lisbon, classifying products by SKU type and turnover, besides streamlining the preparation and consolidation of orders. The warehouse is sectored into five different areas. In two sectors, set aside for type A products, Mecalux has provided light-duty shelves and live storage for picking, which house products supplied by the automatic single-box dispenser.
In the other two, dedicated to type B and C products, live storage for picking was installed with two attached conveyors and light-duty shelving units for the lower consumption boxes.
Finally, there is an area with pallet racking where reserve pallets are stored.
The automatic conveyor circuit runs through all warehouse zones and moves finished orders to the consolidation area. Operators work by zones, only picking in the area they have been assigned.
Type A product
The picking of A products is done automatically. Operators only replenish items and ensure that there is always stock available so operations can be carried out.
Type A products are consumer products and, in turn, within A products, some SKUs are more in demand than others. For this reason, storage solutions were matched with each particular product.
Those in highest demand are deposited in live storage for boxes. Comprised of roller track platforms, they are on a slight incline, so boxes are displaced by gravity.
Operators remove items from the inside of the first box and place them in the corresponding carton compartment from the automatic box dispenser. The advantage of this storage system is stock reserves are housed on the same level, behind the first box, meaning the product is always there for the taking.
Meanwhile, lower consumption SKUs are warehoused in light-duty shelves. They measure only 2.1 m high, which facilitates access to the boxes that are distributed in the automated system.
Type B products
In this area are the shelves with live picking channels and a circuit of roller conveyors placed alongside, whose function is to move completed orders to the consolidation area.
In parallel to the main conveyor, there is another conveyor with free-moving rollers that acts as a prep table for operators to manually move the boxes to the most comfortable position.
This zone is sectored and a different operator works in each sector. Using a radiofrequency terminal, operators identify the order they are going to work with, and the warehouse management software (WMS) tells them what products they need. Then, they collect the products from the shelves arranged on both sides and put the items inside the picking container.
Once finished, they leave it on the main conveyor, so it flows to the next sector if more product is required. Otherwise, it moves towards the consolidation area.
Replenishment takes place in the loading aisle, on the opposite side from the picking tasks. Operators introduce the boxes into the corresponding level, and these move autonomously to the opposite end.
Type C products
Very low turnover products are mostly stored on light-duty shelving units. This ergonomic solution facilitates the classification of products and the picking of orders.
Live storage for picking has also been installed and, in the same way as the sector containing B products, a conveyor circuit runs along the lower level.
Operations are also very similar, but in this case, the operators of each sector crisscross the aisles assigned to them to pick the items from the shelves and place them into the order picking container. Subsequently, the conveyors transfer the completed order to the consolidation area.
Reserve stock
Although live storage for picking holds a part of the reserve boxes, the rest of the products is stored on pallets in upper levels of pallet racking in specific areas.
Levels with pallets, which face the picking aisle, have stops and protective mesh in place to avoid the accidental fall of merchandise.
The pallet racking system provides direct access to the SKUs, which streamlines storage tasks and guarantees a perfect stock control, since a single product is deposited in each location.
Advantages for Alliance Healthcare
- Adaptable operations: the sectored warehouse is highly flexible in terms of picking orders, as each area is assigned a number of shelves and operators.
- Efficient order picking system: the distribution of the goods, according to their characteristics and demand, optimises the movements of the operators and maximises picking.
- Access to merchandise: direct access to the products is essential to speed up picking.
The logistics centre of Alliance Healthcare | |
---|---|
Storage system: | Pallet racking |
Storage system: | Live storage for picking |
Storage system: | Light-duty shelves |
Gallery
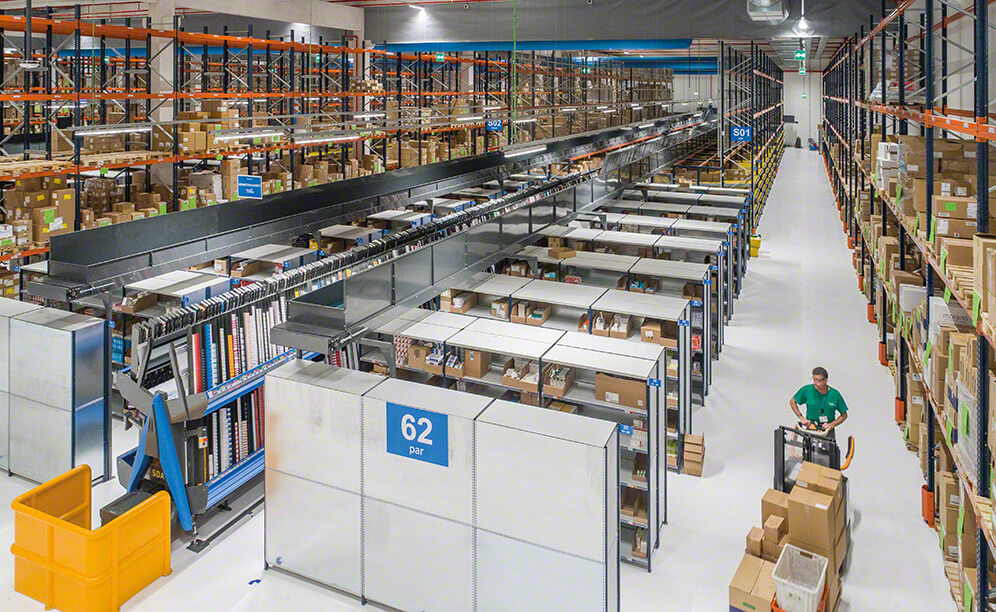
Mecalux has provided all the storage equipment that makes up the installation: light-duty shelves, live storage for picking and pallet racks
Ask an expert