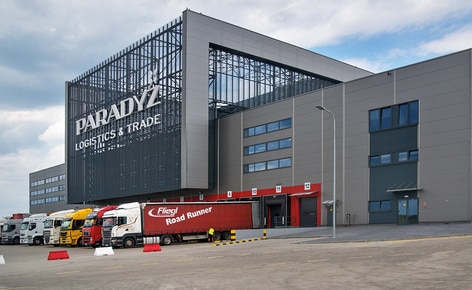
Ceramika Paradyż strengthens its commitment to cutting-edge technologies with a new automated clad-rack warehouse in Poland
High capacity and picking speeds in the automated clad-rack warehouse of Ceramika Paradyż
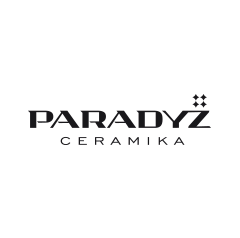
Mecalux has designed Ceramika Paradyż an automated clad-rack warehouse with a capacity for more than 20,200 pallets in the town of Tomaszów Mazowiecki (Poland).The front of the warehouse is a two-storey building to efficiently organise the incoming and outgoing goods, all the while streamlining order prep. The installation supply included the Easy WMS warehouse management software by Mecalux.
The needs of Ceramika Paradyż
Ceramika Paradyż is a leading Polish ceramics manufacturer who exports its products to more than 50 countries around the world. The company is known for introducing the latest technology in its production processes, to deliver innovative products of the highest quality.
To strengthen its growth in the future, the business hired Mecalux to construct a high-capacity automated warehouse, which included a picking area where orders are prepared speedily.
Mecalux's solution
After studying the prerequisites of Ceramika Paradyż in depth, Mecalux's technical team designed and built an automated clad-rack warehouse that meets the requirements set out by the company.
The warehouse is 25 m high, 97 m long and 35 m wide and consists of eight aisles with single-depth racking on each side.
With this solution, the company has achieved the storage capacity needed to supply its market, located primarily within Europe.
A shorter building, attached to the warehouse, was constructed with a two-floor distribution where different operations are performed.
On the lower level are the inputs and outputs of the goods. Checkpoints, a full pallet stacker and an empty pallet dispenser were installed, as well as preload channels.
On the upper level, orders are prepared. There is an entire area set up and equipped with an electric monorail circuit, transfer cars, picking stations, a pallet buffer, as well as a consolidation and wrapping zone.
The warehouse
The 3,290 m2 warehouse is composed of eight aisle with single-depth racking on both sides. In length, there is a total of 45 bays with fourteen levels, with each level accommodating two pallets.
SKUs are deposited in the location based on the A, B and C turnover criteria, all which enables the streamlined movements of the handling equipment.
The racking must withstand its own weight, that of the goods, as well as the wall and roof covering owing to the self-supporting construction. When designing a warehouse of these characteristics, one must take into account factors that interact with the structure, such as the force of the wind, the seismicity corresponding to the area in question and the local building regulations in force.
Warehouse entry and exitThere are two levels for the entry and exit of goods. The bottom one coincides with the ground floor of the annexe building where the entry of goods from the production centre takes place, and the output of full pallets and completed orders towards the dispatch area.
On the top floor, which also coincides with the upper level of the outbuilding, the output of pallets required for picking and the entry of completed orders is performed.
In each aisle, the stacker cranes move the goods from the input and output levels to the locations on the racks that have been assigned by the warehouse management software, the Easy WMS.
This equipment is single-mast MT3 models and work at a travel speed of 220 m/min and 54-66 m/min when raised.
Upper floor: picking area
The top floor of the warehouse annexe is entirely designed for picking. This large area is made up of six picking stations, with the possibly of four more which could be set up in the future, depending on the demands and logistical needs of Ceramika Paradyż.
There is auxiliary equipment on hand to facilitate the manoeuvres of the operators, such as tables that rise to an ergonomic position and vacuum box handlers to move the heaviest loads.
Accurate organisation and the incorporation of automatic equipment are essential to ensure the required cycles and optimal picking performance. The electric monorails collect pallets coming from the warehouse directly from the exit combs and place them in one of four input conveyors to this area.
Two double transfer cars organise this area and distribute the pallets between input conveyors, wait stations and picking stations. The source pallets from which picking has already been performed, go the same route but in reverse to return to the warehouse.
A buffer was enabled with 120 pallet positions for high-turnover pallets. These remain on-hold to avoid unnecessary movements of the stacker cranes and the constant flow of incoming and outgoing goods on this floor and are managed by two transfer cars.
Two more transfer cars are responsible for supplying the picking stations with empty pallets and collecting orders once they are completed. Thereon, they deposit them onto conveyors that connect with the electric monorail, which takes them to the consolidation area, located on one side.
Next to the consolidation area, they have installed manual picking shelves where accessories are prepared for orders as required.
After completing the orders, the pallets are transferred to the stretch wrapper. Later, the goods remain on-hold, waiting to be sent to preloads when necessary.
Automatic connectionThe different areas found on the picking level are connected automatically by electric monorail and transfer car circuits.
The transfer cars, whose task is to form a straight link to the various picking stations and posts, are integrated into the picking area.
The big advantage is that they can move in both directions and join different stations. They run on rails at a speed of 120 m/min and incorporate chain and roller conveyors, as well as telescopic forks for moving pallets.
The electric monorails circulate in a closed circuit surrounding the picking area and connect this area to the entry and exit points of the warehouse and to consolidation.
The electrified monorail system was chosen because it is a very quick transport system that guarantees a steady flow of goods. It can move along curves, and there is the possibility of installing detours and shortcuts.
A maintenance area was designed on one side of the circuit where the trolleys are sent when they require manual intervention. By keeping the floor obstacle-free, the electric monorails facilitate clean-up.
Reception areaThe bottom floor of the warehouse annexe is distributed as follows:
- Input conveyors
- Set of full pallet stackers and empty pallet dispensers
- Pallet reconditioning and checkpoint
- Double recirculation circuit and junction with conveyors inside the warehouse
- Preload channels
- Full pallet unstacker and empty pallet stacker
- Sorting transfer car
- Unloading and shipping docks
The goods from production enter the logistics centre through raised docks. The unloading of the lorries is done by forklifts that let pallets enter the input circuit directly.
In this warehouse, most pallets are of poor quality and products are hefty. Therefore, a set of full pallet stackers was installed that deposit the goods on slave pallets.
Next, the goods go through the checkpoint to validate that they meet the established requirements of the project and enter the warehouse.
Warehouse outputsPallets ready for shipment also leave the warehouse on the lower level and connect to the primary conveyor circuit that moves them to the dispatch area.
A double transfer car moves the loaded pallets and classifies them into twelve preload channels. They consist of chain conveyors and a turntable at the ends that enable the pallets to be collected off the most convenient side, depending on their placement in the transport vehicle.
This system allows the grouping of pallets of the same order or route, and streamlining the distribution lorry loading.
Easy WMS by Mecalux
The Easy WMS warehouse management software by Mecalux was implemented in the logistics centre of Ceramika Paradyż, whose mission is to manage all internal operations.
Because the warehouse is completely automated, the Galileo control module was also implemented; responsible for ensuring the proper functioning of all the devices in motion, as well as fulfilling safety measures.
The Easy Mecalux WMS is in constant two-way communication with the ERP of Ceramika Paradyż; both transferring essential data and information to operate and manage storage effectively and achieve maximum profitability of logistics processes.
Advantages for Ceramika Paradyż
- Maximum throughput: the automated Ceramika Paradyż warehouse establishes a steady flow of products and a flexible order picking system with minimal operator intervention, which eliminates risks.
- Mega storage capacity: the 3,290 m2, 25 m tall clad-rack warehouse can encompass more than 20,200 pallets with a maximum weight of 1,500 kg.
- Potent warehouse management: warehouse operations are managed and organised by the Easy WMS by Mecalux and the Galileo control software whose function is to give movement commands to all devices within the installation.
Automated clad-rack Ceramika Paradyż Sp. z o.o. warehouse | |
---|---|
Storage capacity: | 20,256 pallets |
Pallet sizes: | 800 x 1,200 mm and 800 x 1,250 mm |
Max. pallet weight: | 1,500 kg |
Warehouse length: | 97 m |
Warehouse width: | 35 m |
Warehouse height: | 25 m |
No. of storage aisles: | 8 |
Gallery
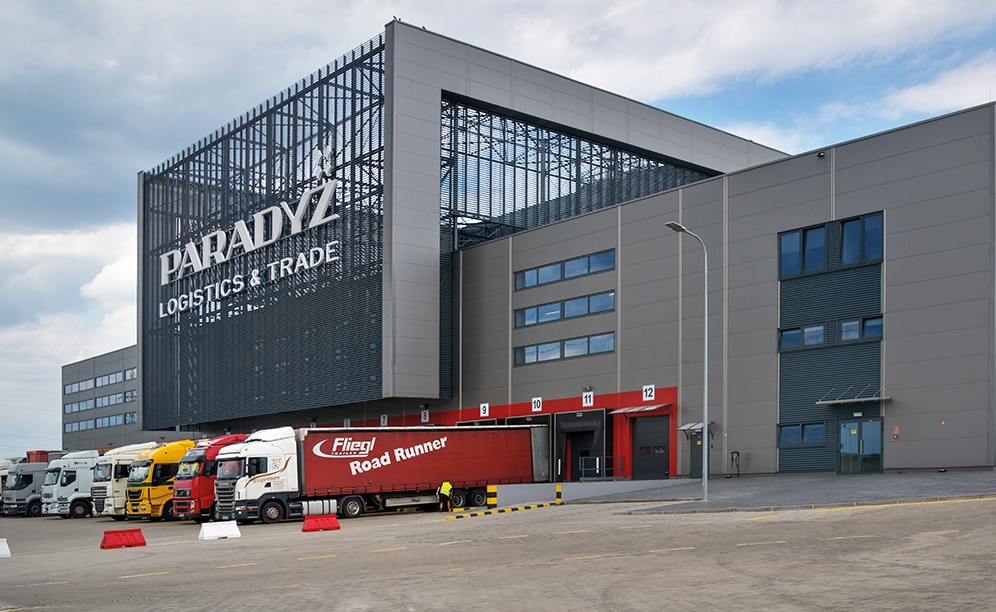
Mecalux has designed Ceramika Paradyż an automated clad-rack warehouse with a capacity for more than 20,200 pallets
Ask an expert