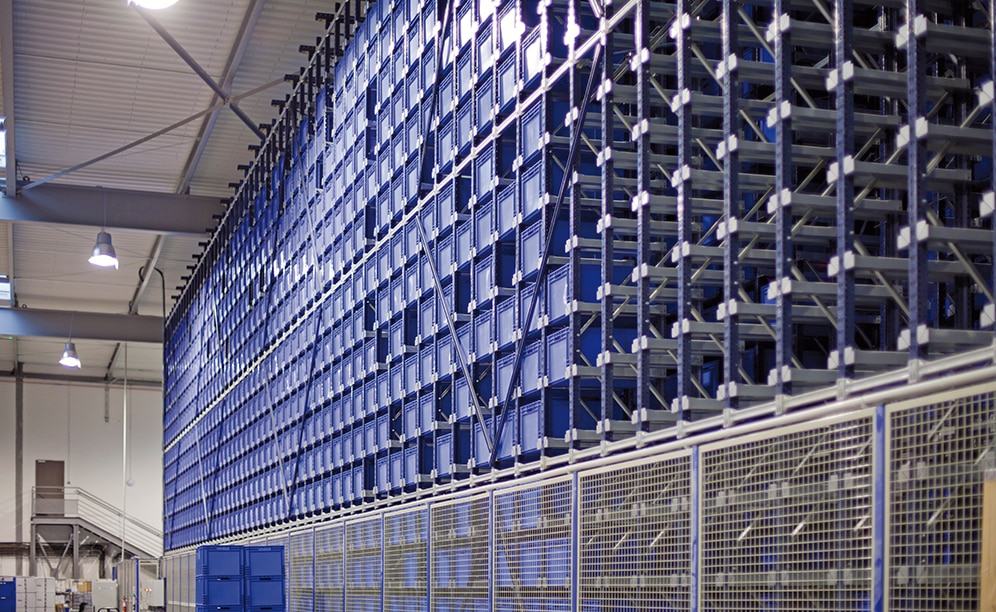
Multiple solutions for the storage and picking of boxes and pallets of locksmithing items
The distributor Cogeferm combines automated and manual systems in its new Paris logistics centre
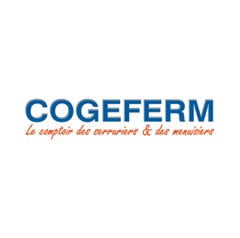
Cogeferm is a French company specialised in the distribution of locksmith supplies and accessories. It has entrusted Mecalux to undertake the design, supply and assembly of the different storage systems in its new 3,000 m² logistics centre close to Paris. Among the featured storage solutions is an automated miniload warehouse. In addition, Mecalux implemented its Easy WMS warehouse management system, which Cogeferm uses to control all processes from incoming goods to outgoing dispatched orders.
Parts of the warehouse: different solutions
This medium sized warehouse is an example for all those logistics centres who focus on the preparation of small and medium sized orders and that require different storage systems, depending on the product type and its consumption.
The Cogeferm warehouse is composed of the following parts:
- Automated miniload warehouse
- Live racking for boxes
- Live racking for pallets
- Automatic box conveyor
- Pallet racking
- Static racking with shelves
- Cantilever racking
The automated miniload warehouse was set aside mainly for order preparation of either small sized and low turnover products (type C), and some medium turnover products (type B). There are two aisles, with the possibility of adding another to adapt to the company’s future growth.
The warehouse with live racking is composed of two racking blocks, separated by a common passageway and set up to house boxes and pallets. They are used for high turnover goods (type A). Reserves of each product are placed on the upper part of the racks.
The warehouse with traditional systems is composed of:
- Pallet racking to store pallets with medium sized products.
- Manual picking racks allocated to odd-shaped products.
- Cantilever racking for extra-long products (profiles, pipes, etc.).
In addition to all the implemented solutions, a space was enabled for consolidating orders, reception and dispatch of goods.
Miniload warehouse operations
It is made up of two aisles with single-depth racking placed on both sides, and two stacker cranes that move along each of the storage aisles to automatically insert and extract boxes. The main conveyor circuit offers an extensive capacity for moving boxes and has two ‘U’ shaped picking stations connected via the recirculation conveyors.
The workflow required by Cogeferm was reached thanks to the stacker crane moving two boxes at a time, both incoming and outgoing. In the future, with the incorporation of the third miniload and the new picking station a 50% increase in cycles/hour is possible.
All processes related to picking begin in this area and are guided by the Mecalux Easy WMS warehouse management system. The first step is placing the boxes in the order prep positions located at the back and that also form part of the conveyor. Once the operator, who works with orders by waves, has finished introducing all the products of their order, they send a signal for the box to enter the conveyor circuit and the box moves along to the live picking warehouse. Once there, the operator may repeat the same procedure with the next wave of orders.
Warehouse with live racking
The boxes that are filled with products from this zone arrive through the conveyor coming from the miniload warehouse.
On one side of the aisle, they set up live racking for pallets allocated to consumer products (type A) and that are mainly supplied in full boxes. Altogether, there are 24 channels with double-deep pallet capacity per channel.
On the opposite side, and reserved for type A products extracted from inside boxes, there are 12 live racking bays for boxes with four load levels. Levels two, three and four accommodate on average six SKUs. Meanwhile, level one, located at the bottom, accommodates on average 5 SKUs. There is a sum total of 414 channels, which each store cardboard boxes five deep.
Reserve pallets are placed on the tops of both racks on different levels, with the same products that are used on the levels below.
The automatic conveyor passes through the inside of the racks, between levels one and two. A second conveyor was installed, outside and in parallel to the racks, which is used as a prep table. When orders are completed, they are pushed onto the first conveyor and move to the sorting/consolidation zone. The full cardboard boxes that arrive from the pallets are also inserted on this conveyor.
All products corresponding to the rest of the areas (pallet racking, picking and cantilever racking) are prepared manually, but are also managed via the Easy WMS.
Easy WMS: warehouse management system
The entire management of the different warehouse areas relies on the Easy WMS: warehouse management system by Mecalux, which guides all operations via computer terminals run by radio-frequency.
This powerful system works through multiple parametrisable rules and covers all the different operations that take place in a warehouse; from the entry of the product to its eventual dispatch, passing through stock control and order picking.
The Easy WMS and the Enterprise Resource Planning System (ERP) have a permanent bidirectional connection in order to allow and facilitate the rest of the operations that take place outside the warehouse, which are essential in any business.
Advantages for Cogeferm
- High storage capacity: the Cogeferm miniload warehouse has a 5,320 eurobox capacity of 600 x 400 x 120/320 mm.
- Each product in its place: different storage solutions were installed that adapt to each product type and its consumption.
- Cost savings: Cogeferm has saved in logistics costs thanks to the automation of the movements inside the warehouse.
- Maximum control: the Mecalux Easy WMS software manages all the movements, processes and operations that take place within the warehouse.
Miniload warehouse Cogeferm, France | |
---|---|
Storage capacity: | 5,320 boxes |
Box sizes: | 600 x 400 x 120/320 mm |
Max. weight per box: | 50 kg |
No. of stacker cranes: | 2 |
Load retrieval system: | single-depth |
Picking stations: | 2 |
Warehouse height: | 8.1 m |
Gallery
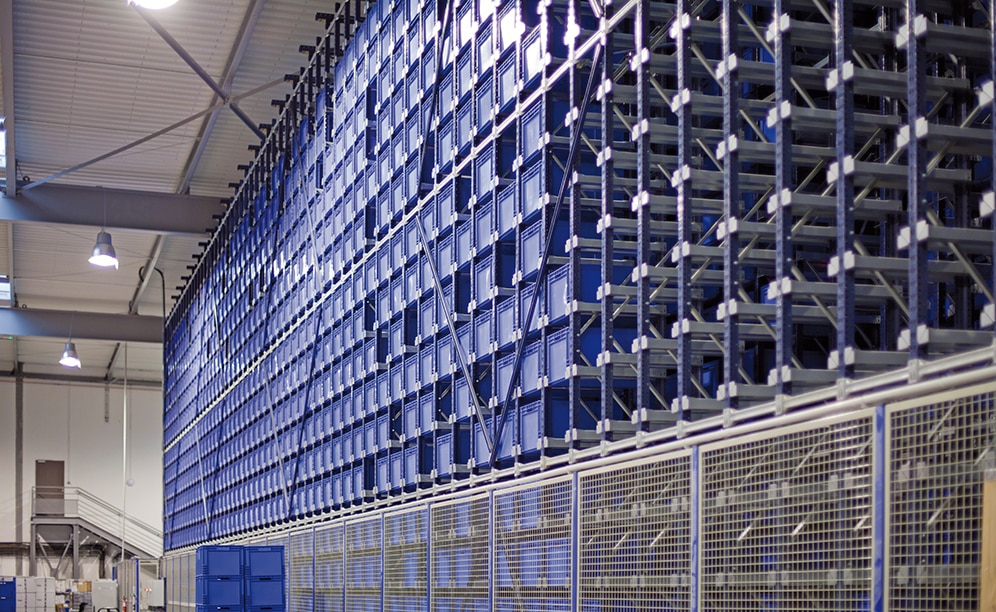
The miniload warehouse is set up to house 5,320 euroboxes of 600 x 400 x 120/320 mm
Ask an expert