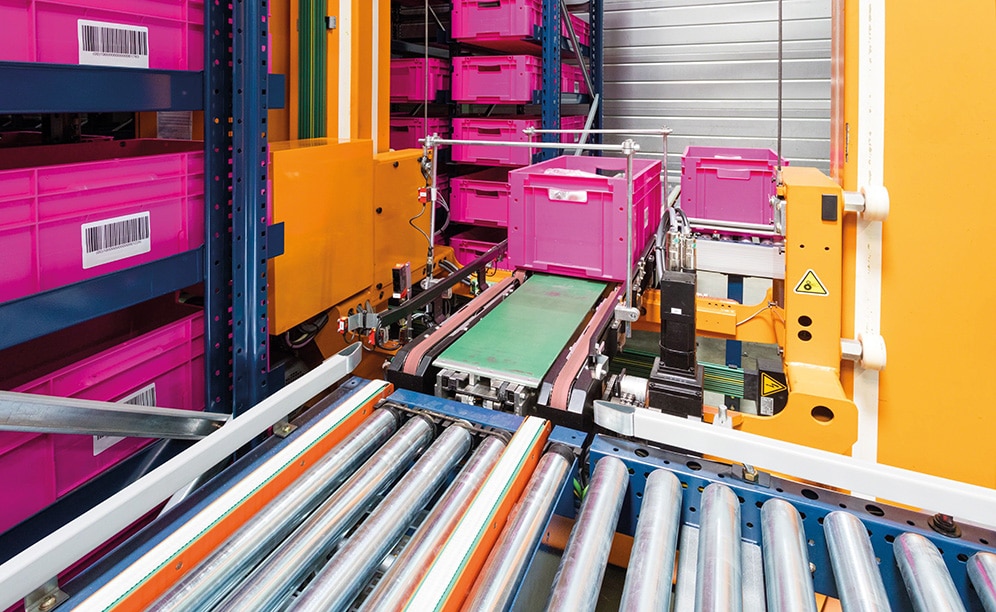
The kitchen and bathroom manufacturer SCD Luisina installs a miniload automated warehouse for boxes in its logistics centre in France to manage more than 1,000 orders a day
An automated warehouse for boxes with the Easy WMS: high efficiency and control at the French manufacturer SCD Luisina
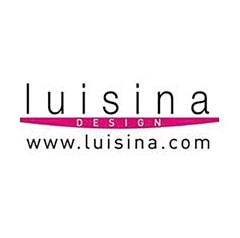
Founded in 1989, SCD Luisina is a company dedicated to the design and distribution of kitchen and bathroom accessories. With more than 1,000 orders a day, the company has relied on the automation offered by the Mecalux miniload warehouse for boxes to manage the logistics process of its centre located in Servon-sur-Vilaine (France). It has also implemented the Easy WMS by Mecalux and the Galileo control programme.
Features of the automated miniload warehouse
The 8 m high warehouse consists of a single aisle with 30 m long, double-depth racking. The 17 level racks contain a storage capacity of more than 4,000 boxes of 600 x 400 x 220/325 mm and a maximum weight of 50 kg each.
A twin-mast stacker crane is in charge of connecting the miniload racks to the conveyor circuit and incorporates a double-box, double-depth extraction system, which can handle two boxes at a time. The extractor picks up boxes from either side with its independently moving blade and double joists. The first box is moved to the opposite side from where the second extraction will be performed.
There is a picking area at the front of the automated warehouse, which links to the miniload racking thanks to a conveyor circuit.
The miniload is an automated storage system for boxes that is an all-in-one installation with racks, stacker crane, conveyors and the warehouse management system. The solution implemented in the SCD Luisina warehouse is ideal for storing and picking according to the "goods-to-person" principle.
Put and pick-to-light racking
These 8 m high shelves, with a capacity for 192 boxes spread over four levels, are used to deposit the items once products from the miniload automated warehouse are picked.
The racks contain the put and pick-to-light system on the side closest to the automated miniload warehouse, so operators know where to leave each item. Once the order is completed, the box is pushed to the opposite side, where a light indicator reports that the order is finished.
Consolidation, packaging and replenishment area
Two conveyor circuits are enabled that connect with the automated miniload warehouse. Empty boxes arrive from the picking area on the top circuit, the operator fills them with the relevant articles and deposits them on the lower circuit which returns to the miniload installation to be stored.
Next to the racks with put and pick-to-light devices, there is the area for consolidation, packaging, labelling and issuance of documentation required for dispatch. Personnel have access to packing boxes of different sizes, prep tables, computers and printers to complete order prep operations.
Easy WMS and Galileo
The warehouse management system, the Easy WMS by Mecalux, is the brain that directs all necessary functions in the general operations within the SCD Luisina warehouse. Some of these functions include:
- Managing incoming goods from receptions.
- Assigning locations of boxes based on consumer and turnover criteria, which aims to achieve maximum productivity.
- Organisation and management of stock.
- Control of the automated miniload warehouse outputs.
- Picking, consolidation, issuing of labels and pre-shipment documentation.
The running of movements is ordered through the Galileo control module, tasked with monitoring all actions that must be performed by the different moving devices to take goods from one point of the warehouse to another.
Pallet racking
Parallel to the miniload installation, there is a 9 m high pallet racking warehouse with an initial capacity of 2,700 pallets.
At lower racking levels, bulkier goods and consumer goods are housed so that the operator can perform picking directly from the pallet. Reserves of each product are stored in upper spaces.
Advantages for SCD Luisina
- Improved storage capacity: the miniload warehouse of SCD Luisina offers a storage capacity of more than 4,000 boxes of 600 x 400 mm.
- Accrual productivity: greater picking speeds thanks to the high degree of warehouse automation.
- Perfect inventory control: the Mecalux Easy WMS and the Galileo control programme manage all the flows, processes and operations that take place within the SCD Luisina warehouse.
Automated miniload warehouse of SCD Luisina in France | |
---|---|
Storage capacity: | 4,032 boxes |
Box sizes: | 600 x 400 x 220 / 325 mm |
Max. weight per box: | 50 kg |
Racking height: | 8 m |
Aisle length: | 30 m |
Gallery
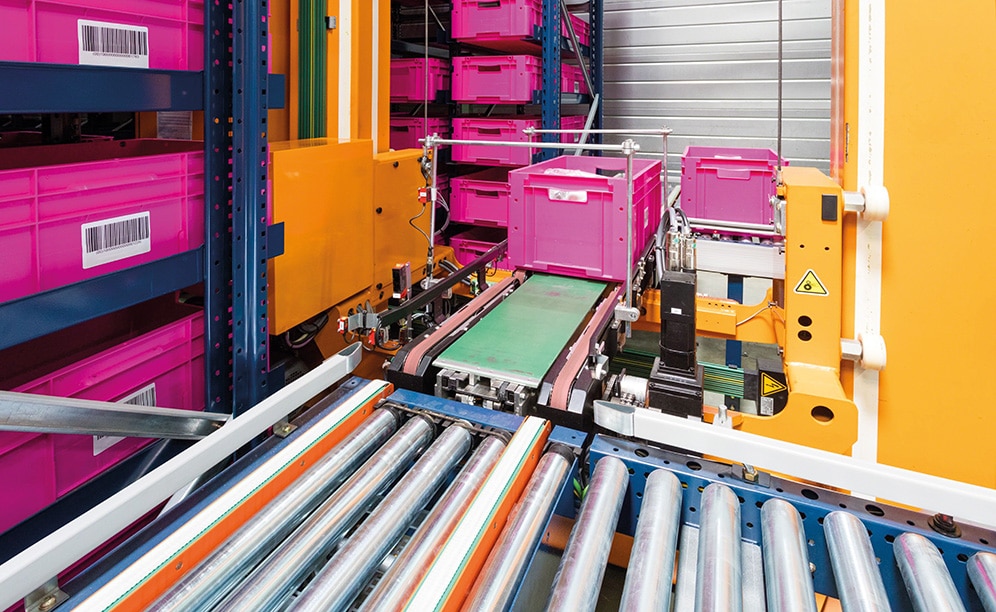
The company has relied on the automation offered by the Mecalux miniload warehouse for boxes to manage the logistics process of its centre located in France
Ask an expert