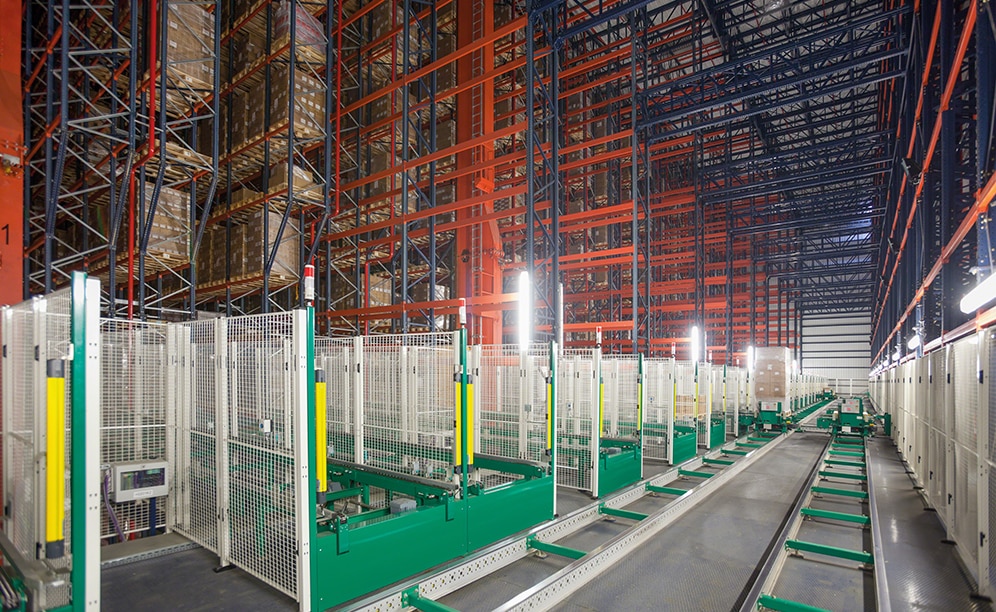
B. Braun, a leading provider of healthcare products, builds its new controlled temperature logistics centre in Tarragona
A new automated clad-rack warehouse with 11 stacker cranes for B. Braun
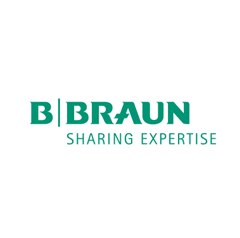
B. Braun has acquired an automated clad-rack warehouse with a 42,116 pallet capacity built by Mecalux in Santa Oliva (Tarragona). The facility enables the company to perform all operations and more than meet their logistical needs.
About B. Braun
B. Braun is an international group with over 175 years of experience in the research, development and supply of health care products and services. Through the past decades, the German company has managed to expand globally and currently does business in over 60 countries.
In 1955 it established itself in Spain, where the company has a team of over 2,000 personnel who produce and distribute medical, surgical and pharmaceutical material. The purpose of procuring the Santa Oliva logistics centre (Tarragona) was to improve its service and fill orders anywhere in Spain and Europe on a very tight deadline.
The new logistics centre
With a floor area of 31,000 m2, the B. Braun logistics centre is divided internally into three buildings:
- The clad-rack facility, which stands out for its height and size, is intended for the storage of pallets. At one end are the input and output circuits that connect to other buildings. On the outside, they installed the main water tank and pumping equipment for the fire-fighting system.
- A two-storey annexe of standard construction. At the bottom, the receipt of the goods is carried out and on top picking operations and the sorting of orders.
- The second annexe, also of standard construction, is used to locate the areas for sorting and consolidation of orders, as well as the shipping docks.
Features of a clad-rack warehouse
The clad-rack warehouse is a solution that makes full use of the surface and height of the edifice to optimise storage capacity. It consists of racking, on which the upper trusses –to which the stacker crane's guides are attached–, the joists of the cladding and the side profiles that make up the walls and the ceiling are fixed in place. The racking supports the ventilation pipes and the temperature control system, the lighting, plumbing and fire sprinkler system.
When designing a warehouse of these characteristics, one must take into account factors that interact with the structure, such as the weight of the building itself, the stored loads, the force transmitted by the wind, overburdening of the roofing (be it snow or maintenance, etc.), the horizontal forces exerted by the stacker cranes, the seismicity corresponding to the area where it is installed, and the building regulations in force in each country.
Inside the automated clad-rack warehouse
The 124.5 m long, 66 m wide, 28 m high clad-rack warehouse contains eleven aisles, six of them with single-depth racking –placed both sides– and five double-depth ones.
The racking is fourteen levels high with a triple-pallet storage depth each. This distribution allows the location of SKUs based on the A, B and C turnover criteria, as well as the streamlining of the movements of handling equipment.
Each aisle is served by a single-mast stacker crane with single and double-deep telescopic forks.
These machines operate at a speed of 180 m/min and 54 m/min when raised and are capable of handling more than 370 pallets per hour.
Stacker cranes move the pallets from the locations to the input and output conveyors located at one end of each aisle.
Height upgrade via trenching
A portion of the clad-rack warehouse was built in a pit in order to not exceed the height stipulated by current legislation while maintaining the required storage capacity.
Two platforms formed by structural profiles are set up to handle pallets on two different warehouse levels: the first set aside for entrances and exits of full pallets and the second to supply areas reserved for picking and sorting orders.
On the lower level, coinciding with the slab or the warehouse floor, they placed computers to control the movements of the auxiliary equipment of the entire installation. Moreover, in this space access for maintenance tasks is set up. Everything is protected and isolated, by means of mesh cladding and safety access doors, from the working aisles where the stacker cranes circulate.
Advantages for B. Braun
- Surface optimised: the clad-rack installation uses the entire surface and height, achieving a storage capacity of 42,116 pallets.
- Automation: the logistics centre is equipped with the latest technology, with eleven stacker cranes capable of handling over 370 pallets per hour.
- Everyday safety: the warehouse is highly automated and equipped with all available safety elements, limiting human intervention while ensuring the safety of personnel in case the facility is accessed.
Automated clad-rack warehouse of B. Braun in Spain | |
---|---|
Storage capacity: | 42,116 pallets |
Warehouse length: | 124.5 m |
Warehouse width: | 66 m |
Warehouse height: | 28 m |
No. of aisles: | 11 |
No. of load levels: | 14 |
Pallet depth per lane: | 3 |
Gallery
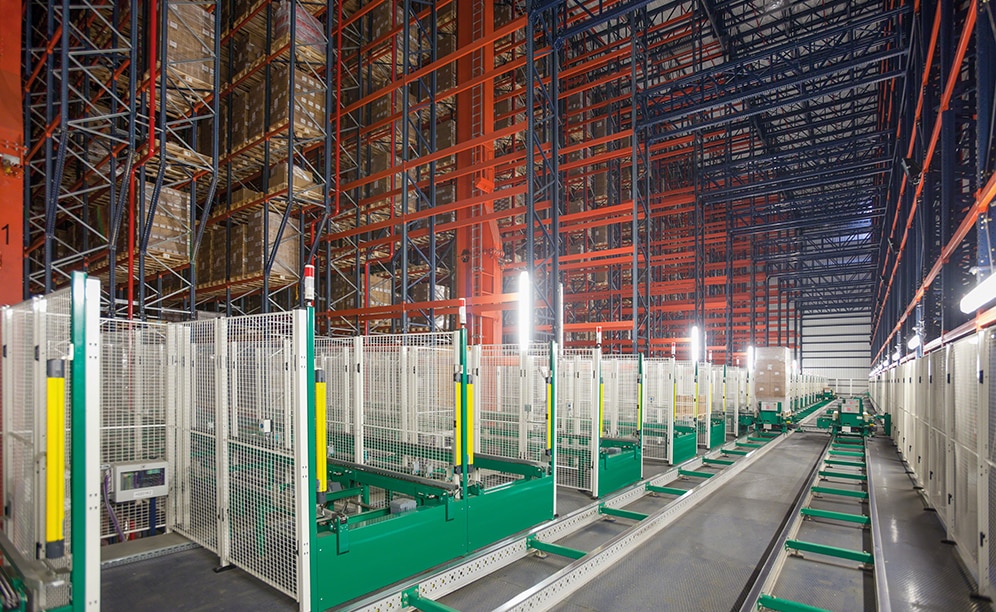
B. Braun has acquired an automated clad-rack warehouse with a 42,116 pallet capacity built by Mecalux
Ask an expert