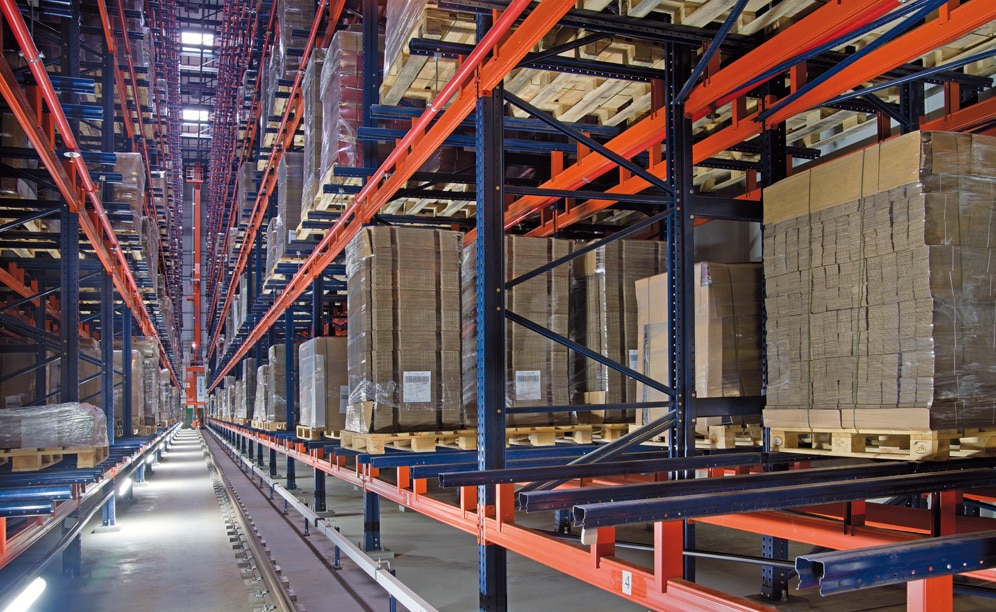
An automated clad-rack warehouse with a capacity to store more than 6,300 pallets in just two working aisles
Customised stacker cranes for the Wok warehouse in Poland
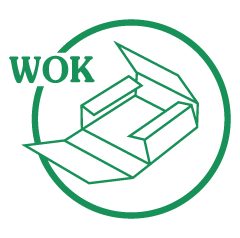
WOK, one of the most well-known packaging companies in Poland, has constructed a new automated clad-rack warehouse with a capacity for more than 6,300 pallets. It is equipped with stacker cranes adapted to the features of the installation and the products stored: they have telescopic forks that can handle up to four pallets deep per aisle side. Its operation is very fast and simple, controlled at all times by the Easy WMS warehouse management software by Mecalux.
Needs of WOK
WOK is a family business dedicated to the manufacture of boxes and cardboard packaging. Founded in 1991 and during its long history, it has focused on the diversification and expansion of its spectrum of products, as well as the automation of work processes to boost productivity and reduce costs.
The company never stops developing new solutions designed to meet their customer's demands. With this objective, in the last few years it decided to overhaul all its production centres and thereby accelerate its expansion in the Polish market.
The company asked for Mecalux's collaboration, aiming to find the ideal storage solution and organise all products pertaining to the production centre in the city of Brodnica (Poland).
Solution by Mecalux
After analysing the logistics needs of WOK, Mecalux constructed a 1,989 m2 clad-rack warehouse with very simple automated operations for the input and output of goods that suit the characteristics of the products.
The warehouse is composed of two, 86.3 m long aisles, with racking where they deposit four pallets deep on each side and which are eight levels high.
Being 23 m high, WOK’s automated warehouse offers a storage capacity of more than 6,300 pallets of 800/1,000 x 1,200 x 1,800/2,000/2,200 mm in size and each a maximum weight of 600 kg.
This is the layout of the warehouse and its operation:
- Product inputs
- Conveyor circuit
- Clad-rack warehouse
- Outputs to dispatch
Clad-rack warehouse
These warehouses are composed of the racks themselves, on whose structure the side cladding and roofing is attached. Many factors must be anticipated when designing the building, such as the loads of the goods stored, the forces exerted by handling equipment, the force of the wind, the seismic coefficient corresponding to the area where it is installed or the local regulations in force. All these factors are duly taken into account when calculating and drawing up a new facility.
Functional operations
The warehouse stands out because of its functionality. The input and output of products is done automatically, via a conveyor circuit with rollers and chains that controls the pallets at all time from their reception. This system allows load units to move with great agility, without the need for human intervention and avoiding all logistical errors.
Once operators deposit pallets on the entry conveyor, these pass through the checkpoint to validate that its weight, size and state comply with the system's requirements. Goods that do not pass inspection are directed to the conveyor for rejected pallets, which is set up in parallel; the pallet is removed from the circuit and reconditioned to enable its entry into the warehouse.
Fire safety systems
The fire safety system is a priority for the type of products stored, the characteristics of the installation and compliance with local fire prevention and safety regulations.
There are smoke detectors and control devices that take action, if needed, directly above the affected area. The automatic sprinklers are placed strategically inside the racking.
Adapted stacker cranes
The warehouse is equipped with racks where pallets are placed four deep per level. This solution is adapted to the capacity needs of the company and to the features of its product, with load units that do not exceed 600 kg in weight.
A stacker crane operates in each aisle at a travel speed of 220 m/min and a 66 m/min lift speed. This allows dynamic handling of goods to achieve the product flows required by the company.
On the other hand, warehouse inputs and outputs are separated to avoid interference between the two operations. The front of the warehouse is set up with a circuit for already prepared goods to facilitate their dispatch.
An intelligent software
The Mecalux Easy WMS warehouse management software governs the warehouse. It is the nerve centre that coordinates and directs all operations carried out in the installation, which include: reception, identifying goods and validating their characteristics; the storage process, such as locating the pallets in the racks based on rules and algorithms; and dispatch, grouping output orders based on their destination.
The software is in permanent and bidirectional communication with the company’s SAP ERP. They transfer data and information, which is indispensable for warehouse management with great efficiency and capitalise on all the logistics processes that they implement.
Being completely automated, the Galileo control module was installed that takes charge of giving commands to all the movements of the equipment, stacker cranes and conveyors. At the same time, it guarantees maximum safety of the warehouse.
Advantages for WOK
- Large capacity: WOK's new clad-rack warehouse has the capacity for more than 6,300 pallets of different sizes and a top weight of 600 kg.
- Maximum speed: its operation is very simple, dynamic and completely automated, with minimal human intervention and without logistical errors.
- More efficient management: the implementation of the Easy WMS by Mecalux and the Galileo module entails saving in logistics costs, improves the quality of service and maximises warehouse productivity.
Automated clad-rack warehouse | |
---|---|
Storage capacity:: | 6,352 pallets |
Maximum weight per pallet:: | 600 kg |
Pallet sizes:: | 800/1,000 x 1,200 x 1,800/2,000/2,200 mm |
Levels high:: | 8 |
Racking length:: | 77.6 m |
Racking height:: | 21.7 m |
Gallery
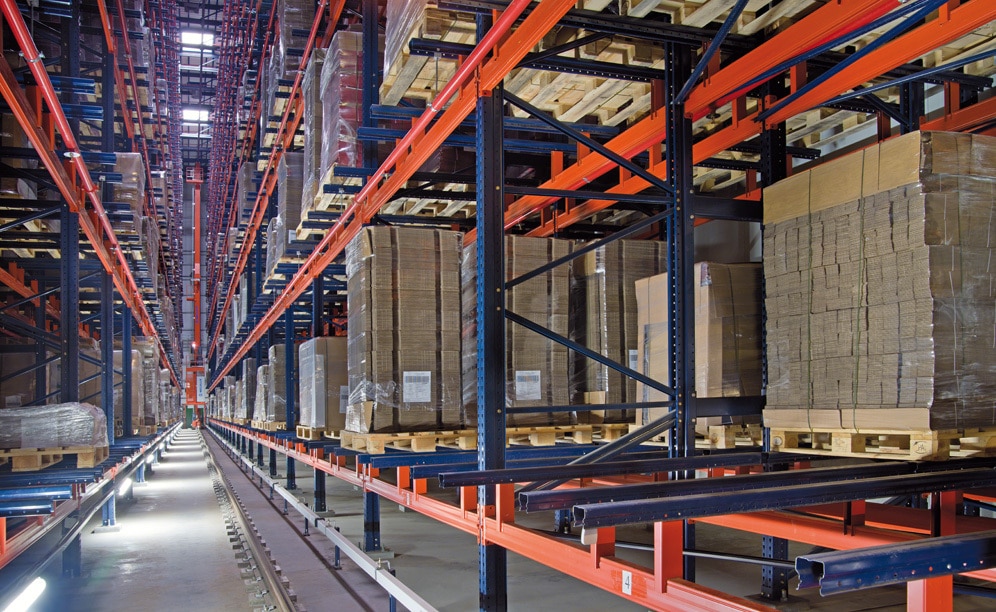
A new automated and clad-rack warehouse for WOK in Poland, with customised stacker cranes
Ask an expert