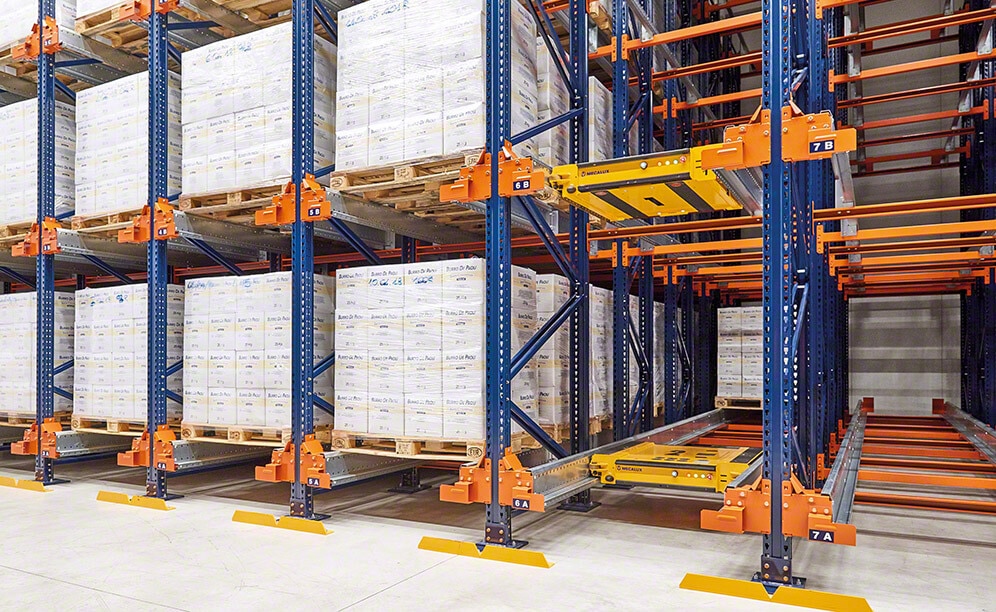
An Italian butter manufacturer boost its efficiency with the installation of two frozen storage chambers with the high-density Pallet Shuttle system
Twin frozen butter warehouses operate with the Pallet Shuttle system at Burro De Paoli
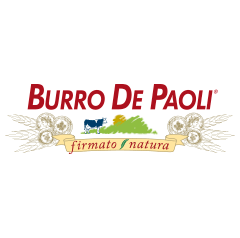
The butter producer Burro De Paoli has equipped both its frozen storage chambers in Italy with the semi-automatic Pallet Shuttle system. The installed storage solution boosts productivity, provides a 1,494 pallet capacity and minimises the workforce.
About Burro De Paoli
This Italian business has more than 50 years of experience in butter production. Its product catalogue offers a host of cheeses and butter.
Butter making at Burro De Paoli brings together traditional, home-style recipes and high-tech machinery, as well as the strictest quality control standards that guarantee excellence.
High-density Pallet Shuttle system
Mecalux set up the Pallet Shuttle system in the two frozen storage chambers Burro De Paoli owns and operates in Vicenza (Northern Italy). Chamber 1 is comprised of a pair of 170 m² blocks, which hold finished products. Chamber 2, enabled with a single 161 m² block, stores semi-finished products. Both areas are run at a controlled temperature of -25 ºC.
The Pallet Shuttle is part of a high-density system that makes full use of the physical warehouse space, cutting down on the number of aisles. In addition, given that an operator does not need to enter the lanes with the forklift, the insertion and extraction of goods are very swift.
With a total of 174 channels, the Burro De Paoli warehouse has a capacity to hold 1,494 pallets of 800 x 1,200 mm. Each of these can weigh 1,200 kg. Racks are 7.5 m high, and their uprights are protected from rough handling by machinery. When calculating the rack the seismic action was taken into account, applying the corresponding local regulation.
To store pallets, the operator places the electric shuttle in the corresponding channel by means of a reach truck. Later, the pallet is deposited in the first rack position letting the shuttle shift it to the next free location automatically. Pallet extractions are done via this process but in reverse.
Imerio De Paoli - Production & Logistics Manager at Burro De Paoli
"The Pallet Shuttle system by Mecalux has let us use all the space in our cold storage chambers, which run at sub-zero temperatures. On top of that, we have streamlined the storage of goods by not having to drive into the warehouse lanes with a forklift."
FIFO system: channels and batches
Goods management is carried out according to the FIFO criterion by batches or channels. The first channel to be filled with a SKU is the first to be emptied, thus assuring product rotation.
Tablets: how they work
The operator sends movement orders to the Pallet Shuttle through a Wi-Fi connected tablet. Its intuitive interface provides the operator with information about the number of pallets stored in a channel. Here are some of the operations that can be run from this device:
- Select shuttles in operation and verify their status.
- Choose which pallets to operate with.
- Continuously load and unload goods from the channels.
- Inventory control: information about the stored pallets shows on the tablet.
- Locate shuttles via audible and light signals.
- Improve operational safety. Use the tablet to activate the locking system that attaches the shuttle to the forklift’s forks and prevents it from accidentally falling.
Easy battery recharging
The shuttle includes a battery level indicator and additional backup energy. Moreover, spare batteries were provided to power the equipment while the two Pallet Shuttles keep working.
Batteries are extracted from the shuttles and connected by just slipping them into the charging stations set up in the warehouse. There is also a separate cable that lets the shuttle itself be charged, without needing to remove the battery.
Advantages for Burro De Paoli
- Large storage capacity: the Pallet Shuttle system moves inside high-density racks, boosting the maximum storage capacity.
- Operational optimisation: the motorised shuttle frees the operator from entering the racks with a forklift. This semi-automatic system reaches different depths at any point of the rack levels.
- Efficient goods management: having both chambers at -25 ºC and using the FIFO management criterion by batches or channels mean goods arrive at the consumer in better condition.
Frozen storage chambers | |
---|---|
Storage capacity: | 1,494 pallets |
Pallet size: | 800 x 1,200 mm |
Max. pallet weight: | 1,200 kg |
Racking height: | 7.5 m |
Warehouse temperature: | -25 °C |
Gallery
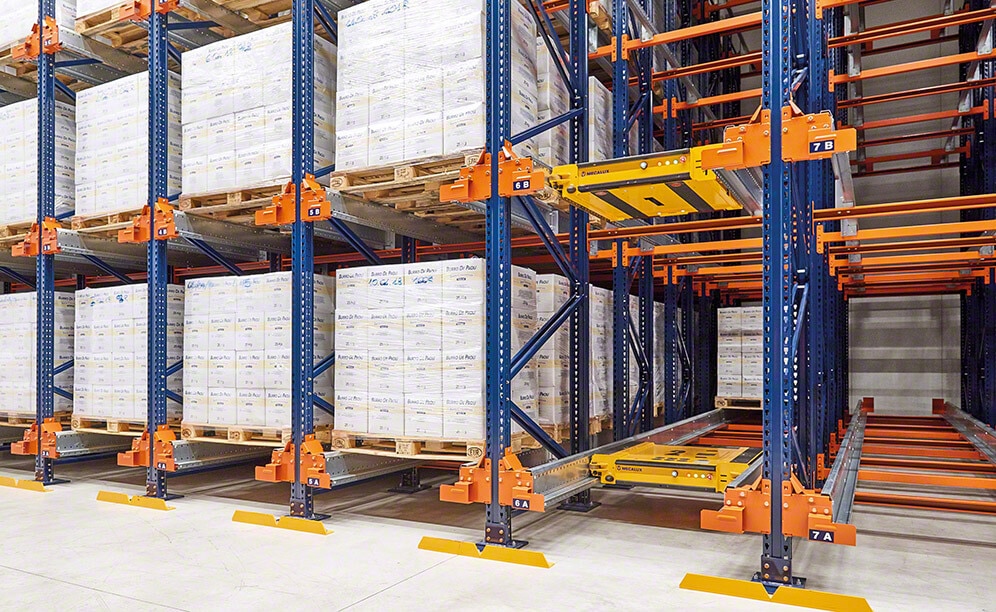
Mecalux set up the Pallet Shuttle system in the two frozen storage chambers Burro De Paoli
Ask an expert