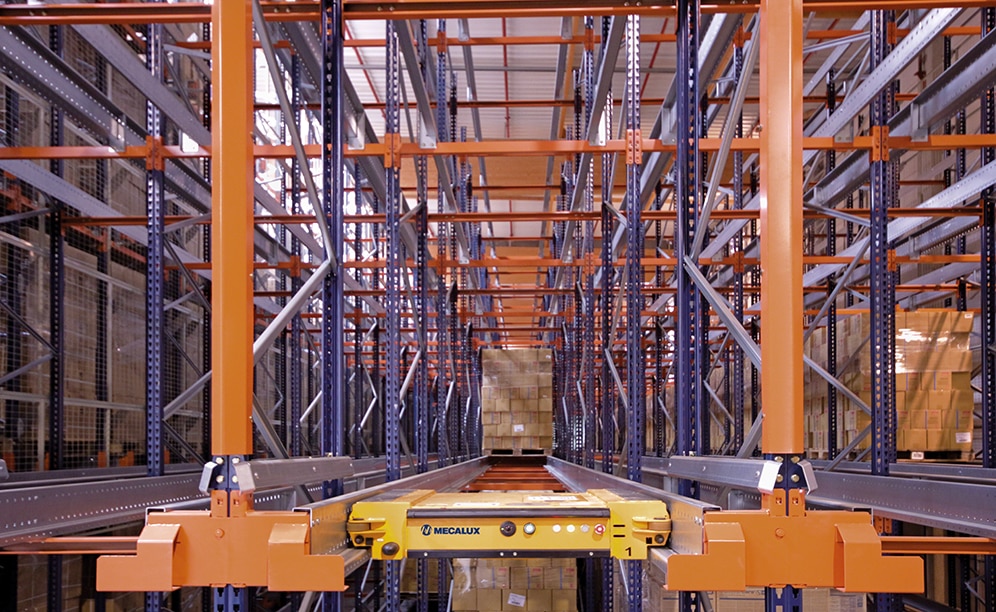
The high-density Pallet Shuttle system multiplies efficiency in the supply of medical devices
Didactic improves the productivity of its Normandy warehouse with Pallet Shuttle
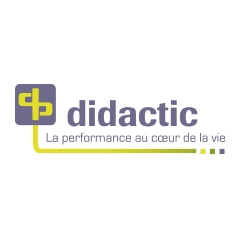
Mecalux has provided the Pallet Shuttle system in the Didactic warehouse in France. The company, specialised in manufacturing medical diagnostic equipment, expanded its warehouse to incorporate the sterilisation process of its products. Installing this storage system improves productivity, obtains more capacity and reduces personnel costs.
About Didactic
Didactic is the leading supplier of sterile medical devices in public and private health centres in France. With over 40 years of experience, it has become a leader in the development of devices and instruments used to perform medical tests.
The company in known for its spirit of improvement and the constant search for new and innovative solutions to capitalise the overall performance of its services, including the manufacture of products, sterilisation, logistics, distribution and marketing.
The needs of Didactic
The company required the expansion of its warehouse in the town of Étainhus (Normandy). Previously, they had pallet racking, also supplied by Mecalux, for the storage of products from its various manufacturing plants. However, they needed to accommodate new products and incorporate the sterilisation process in the same installation.
Didactic was looking for a suitable solution to deposit goods, perform sterilisation processes, verify the quality of the products and dispatch them as quickly as possible, in a continuous flow without interference in operations.
For that reason, the customer requested the collaboration of Mecalux to carry out the expansion project and find the most appropriate storage system to maximise the available surface, to obtain high capacity and, in turn, to expedite the entry and exit of the pallets.
The expansion
To meet Didactic's requirements, Mecalux supplied six blocks of 10 m tall high-density racks with a capacity for more than 3,700 pallets of 800 x 1200 mm. Each block has very different functions and applications depending on the workflows and product features:
- Blocks 1, 2, 3 and 4, which are 7 m and 12.1 m deep, are allocated to products from the loading docks, ready to move onto the sterilisation area.
- Block 5, with 12.1 m deep channels, is set aside for products that have completed the sterilisation process, pending verification and quality control.
- Block 6 is 48 m deep. The pallets deposited here have passed inspection and are removed for dispatch, according to the FIFO criterion (first in, first out).
The six racking blocks are four levels high. The racking structure is adapted so electric shuttles can move autonomously via the interior of the channel storage, ensuring a constant flow of goods. Thus, forklifts do not need to enter the storage aisles.
Pallet racking
Before the expansion, the warehouse was comprised of eleven double and one single pallet racking attached to the wall for products processed in other manufacturing plants, which were kept as part of the extension.
These racks are characterised by their versatility to accommodate pallets of different sizes and turnovers, and for providing direct access. This affords flexibility in managing goods and facilitates perfect stock control as each location is earmarked for a particular pallet.
The sterilisation procedure
The sterilisation of Didactic's products is one of the most critical processes that takes place in the new enlarged zone of the logistics centre.
First, the goods in blocks 1, 2, 3 and 4 are moved to the sterilisation area located directly opposite. Once this process is finished, the pallets are deposited in block 5 in quarantine. They are stored for a time while the necessary tests that ensure product asepsis are performed.
Then, the goods that pass the quality control are sent to block 6. These very deep racks meet FIFO criterion: the pallets are introduced into the loading aisle, removed from the opposite –dispatch side– and routed to the shipping docks. With this system, interference between inputs and outputs is eliminated.
The Pallet Shuttle system
This system uses available space to provide greater storage capacity.
Its operation is quick, simple and requires minimal movements: the operators place the motorised shuttle into the channel, they deposit the pallets into the first position of the racks, and the Pallet Shuttle autonomously transfers them directly to the first free location. When removing the goods, the same process takes place but in the reverse order.
The shuttles incorporate cameras and use tablets as monitors that play the images. Thus, the operator visualises the direction and movement of the forks when introducing the Pallet Shuttle into the channel, positioning it correctly and preventing accidents from occurring.
Control tablet
Storage processes are managed with tablets through which orders are given to the Pallet Shuttles. They have a tactile interface and a very intuitive software that requires no special training to use. Each tablet can interact with all the warehouse's shuttles following a prioritisation protocol.
From the tablets, a set of very different functions can be executed, including:
- Selection of the shuttles in operation and verification of their status.
- Choice of pallets to use in operations.
- Continuous loading and unloading of channels.
- Inventory taking to automatically count the number of pallets stored.
- User and authorised personnel management.
- Location of the shuttles by an audible and light signal.
- Activation of the locking system that increases the attachment of the Shuttle Pallet to the forks of the forklift and prevents its accidental fall.
Battery charging
The facility has reserve batteries, so operations are never interrupted. You can load a piece of equipment while the Shuttle Pallet continues to operate in the assigned channels.
Batteries extracted from the shuttles are connected by simply fitting them into the charging stations set up in the warehouse. In addition, there is also a separate cable that lets you directly charge the shuttle, without removing the battery.
Rescue device
If a shuttle breaks down, or the battery runs out when it is inside a channel, another Pallet Shuttle comes to its rescue. An accessory is incorporated into the operating shuttle that joins to the faulty one, and together they move to the channel exit.
A completely safe system
Forklifts do not enter the aisles, so the risk of accidents is virtually nil. In turn, the shuttle is equipped with various electronic and mechanical components that guarantee its smooth operation.
The shuttle has a bumper preventing possible entrapment and crushing, emergency stops that cut the power if necessary and ultrasonic sensors that detect the position of the pallets in the channels.
Furthermore, the Didactic warehouse also features protective mesh panels on the sides of the racking to prevent the accidental fall of goods.
Advantages for Didactic
- Optimal organisation: the distribution of the racking blocks ensures a constant workflow and the correct control of the products' sterilisation process.
- Increased productivity: the system is very fast and with minimal intervention by operators; the Pallet Shuttle performs movements within the channels with total autonomy.
- Safety guaranteed: the Pallet Shuttle and warehouse racking have safety devices for the maximum protection of the structure, the goods and personnel.
Pallet Shuttle system in the Didactic warehouse | |
---|---|
Storage capacity: | +3,700 pallets |
Maximum pallet weight: | 510 kg |
Pallet size: | 800 x 1,200 mm |
No. of channels: | 212 |
Racking height: | 10 m |
Gallery
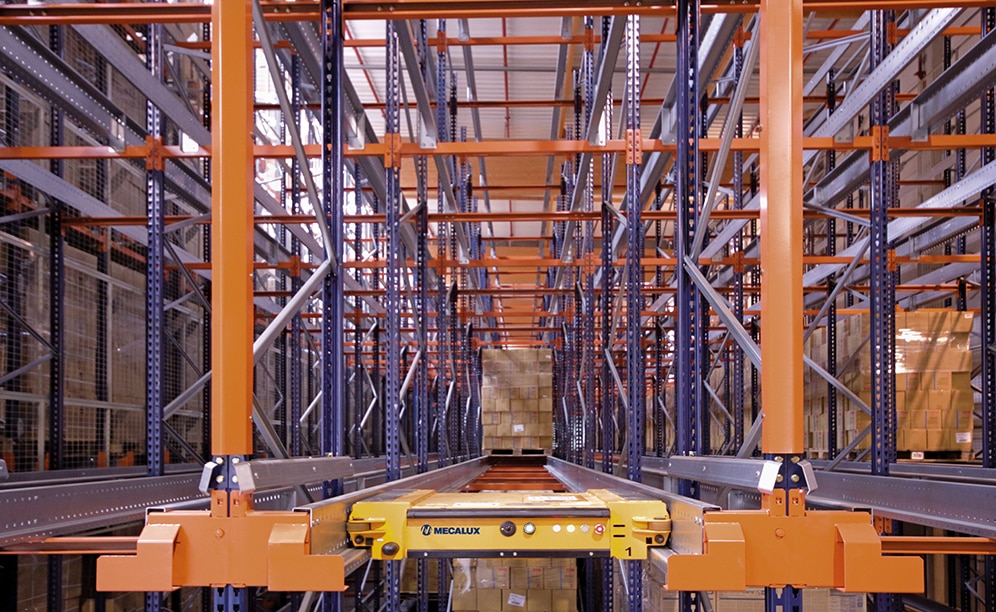
Installing the Pallet Shuttle system improves productivity, obtains more capacity and reduces personnel costs
Ask an expert