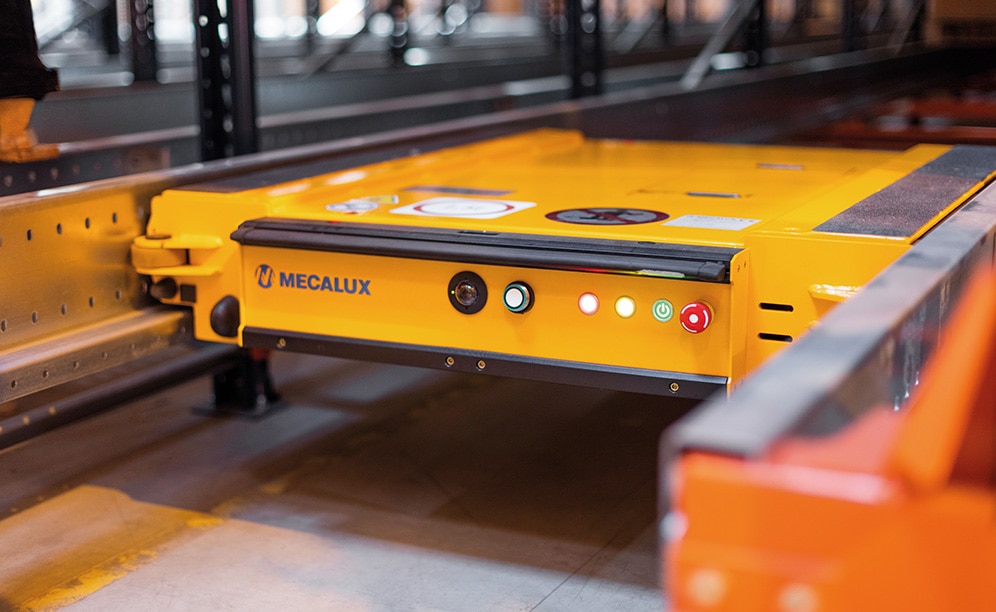
Gémo, a well-known French fashion distributor, combines the high-density semi-automatic Pallet Shuttle with pallet racking and picking shelves to max out throughput
A combination of systems store the numerous SKUs of the fashion distributor Gémo
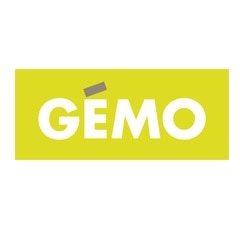
Gémo, a well-known company dedicated to the distribution of clothes, shoes and accessories, has turned to Mecalux for the supply and installation of racks using the Pallet Shuttle system, conventional pallet racking and an area to perform picking tasks at its logistics centre in Beaulieu-sur-Layon (France).
About Gémo
Gémo, a subsidiary of the French group Eram, is a company founded in 1991 and specialises in the distribution of fashion for women, men, children and babies. With highly competitive prices, the company's product selection includes clothing, footwear and accessories.
Over time and after much perseverance, Gémo has become a benchmark in the sector. It currently has 4,400 employees and 500 shops.
The sectored warehouse
Gémo required a warehouse that was set up to manage a large number of products of different sizes and SKUs, and likewise, a solution that would reduce the time spent on picking.
Given these premises, the Gémo installation was divided into three cells. Each of them has the best storage solution enabled to suit the characteristics of each product and the logistical needs of the company:
- Cell 1: floor storage and future expansion.
- Cell 2: high-density racking with Pallet Shuttles.
- Cell 3: pallet racking and manual picking.
Cell 2: Pallet Shuttle system
With a storage capacity for 14,400 pallets of 1,200 x 800 x 1,600 mm and a maximum weight of 350 kg each, this cell is composed of eight blocks of 10.1 m high high-density racks, which have five load levels and are 26 pallets deep. Six such blocks consist of 14 aisles, while the other two have 15.
A 4.5 m wide central aisle passes through the installation, joining the eight blocks that make up this cell. The aisle width is sufficient so that operators can comfortably circulate and manoeuver with forklifts.
To round off operations and streamline the storage process, five Pallet Shuttles move inside the racks following the instructions the operator transmits to it through Wi-Fi connected tablets.
Moreover, as a safety measure, protectors were placed on all the rack uprights that face the working aisles, and an underpass was opened that crosses through the shelves to facilitate the flow of movement between cells and, in turn, to be used as an emergency exit. Also, the racks are protected with mesh to prevent the accidental fall of merchandise.
How de Pallet Shuttle operates
The Pallet Shuttle works as follows:
- The operator inserts the Pallet Shuttle into the channel via a forklift.
- Once the shuttle is in the channel and the pallet loaded, it moves horizontally until it reaches the first open location, where the shuttle deposits the pallet.
- While the shuttle transfers and deposits the pallet, the operator uses the time to place another pallet in the first position of the channel. Thus, when the shuttle returns to the front of the lane, it can consecutively repeat the same movement.
When it has finished loading in a channel, the Pallet Shuttle is moved to the one where it is going to operate next. The extraction is carried out by performing the steps in reverse.
The machines used by operators are high-lifting reach trucks, able to extend to 10 m in height and arrive to the top level of the racks. Frontal stops were installed on the floor of every storage lane, while the input/output storage channels contain centralisers that favour the positioning and centring of the load unit.
Pallet Shuttles are equipped with a positioning camera, which facilitates the insertion and centring of the Pallet Shuttle in the channel, all very useful in high-rise installations. The image from the camera is displayed on the tablet, responsible for controlling all Pallet Shuttle operations with a straightforward and user-friendly interface. Among its most important features are: the selection of the shuttle they are going to operate; automatic and manual execution of maintenance movements; battery charging information; real-time inventory; user management; etc. All this, invariably under the control and management of the WMS used by the customer.
Cell 3: the picking area
Just in front of the pallet racking, there is a zone for picking operations of smaller-sized products. The area is equipped with medium-duty M7 shelves and a space to place the pallets directly on the warehouse floor.
The shelves are ideal for picking in warehouses where the goods are stored and removed manually, providing direct access to the boxes and single units. Levels are formed by mesh shelves that enhance the passage of water in case the fire safety system is activated.
Stacking pallets on the floor is convenient when preparing single SKU orders and those which contain consumer products.
Advantages for Gémo
- High storage capacity: the Gémo warehouse has a total storage capacity of 19,808 pallets.
- Multiplied picking speeds: the cell with medium-duty M7 shelves provides optimised and streamlined movements during picking tasks.
- A wide variety of products: thanks to various solutions installed in the Gémo warehouse, they can store all kinds of products of different sizes and weights.
Cell 2: high-density racking with Pallet Shuttles | |
---|---|
Storage capacity: | 19.808 pallets |
Pallet size: | 800 x 1,200 mm x 1,350 mm / 1,000 x 1,200 mm x 1,300 mm |
Max. pallet weight: | 530 kg |
Warehouse height: | 11 m |
Gallery
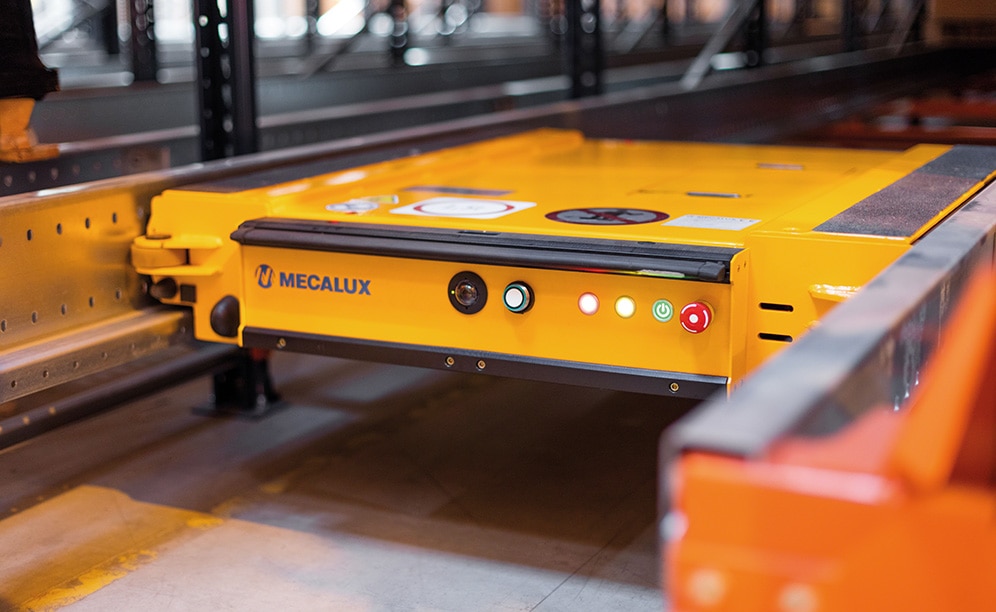
Gémo has turned to Mecalux for the supply and installation of racks using the Pallet Shuttle system
Ask an expert