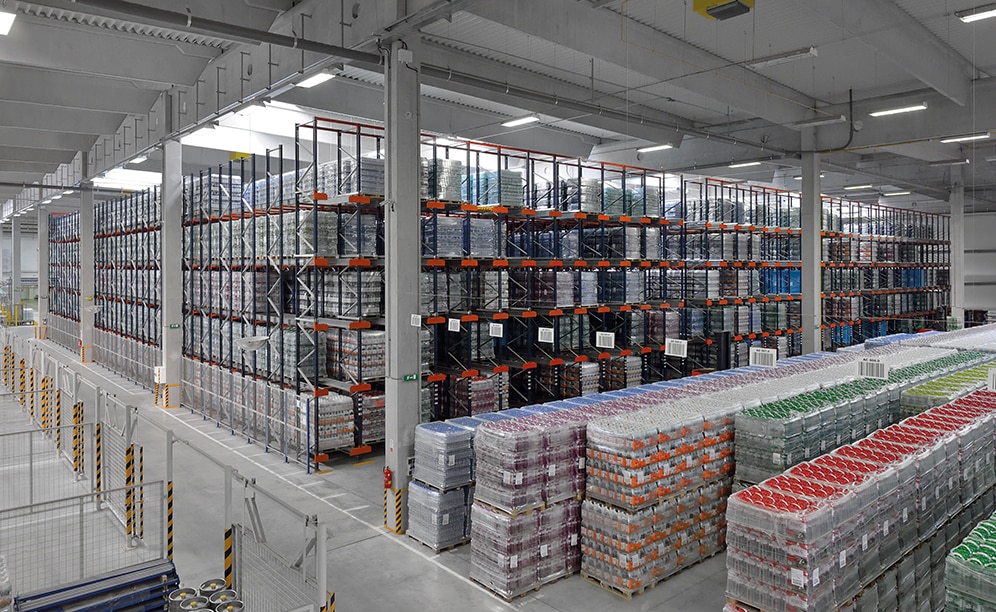
A beverage logistics operator multiplies its capacity with the Pallet Shuttle system and 50 m deep racks
The Slovakian company Santa-Trans fits out its warehouse with the high-density Pallet Shuttle system
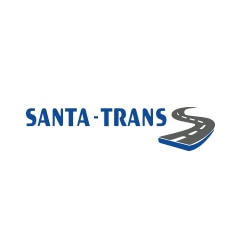
The Santa-Trans company is one of the most renowned non-alcoholic beverage logistics operators in Slovakia, with a presence in Central and Eastern European countries. Recently, the company equipped its warehouse with the semi-automated high-density Pallet Shuttle storage system to optimise both time and space, and increase its productivity.
Mecalux’s proposed solution: the compact Pallet Shuttle system
The project, set up by Mecalux for Santa-Trans, divides the warehouse into two areas: one reserved for consumer products located on the floor, and another equipped with the high-density Pallet Shuttle system for medium and low turnover products.
Consumer products are piled up on the floor of the warehouse in order to make full use of the space. Therefore, operators have fast and easy access to goods, avoiding unnecessary movements. This is possible because goods consist of shrink-wrapped bottles on pallets, making them sufficiently resistant for one pallet to be placed on top of another without fear of the product being damaged.
The compact pallet racking, located just behind this area, is set up for the movement of the Pallet Shuttle and allocated to medium and low turnover products. The most striking characteristic of this Mecalux project is the massive depth of the 50 m long storage channels. The only system able to operate efficiently at such depths is the Pallet Shuttle, which accesses all the racking locations quickly and easily.
What also stands out is the large number of storage channels that result, 195 altogether. These make it possible to locate a different SKU in each channel, fostering product diversification. Considering the required warehouse flows, capacity and channel numbers, the Mecalux technical department estimated that eleven shuttles were needed to achieve proper operations within the installation.
In this case, the racking has also been enabled to follow the FIFO load management technique (First in, First out), by inserting pallets into one side and extracting them from the other, offering perfect product turnover.
Operation of the Pallet Shuttle system
Each Pallet Shuttle acts autonomously following the instructions that the operator transmits. This is done via a RF control unit or a Wi-Fi connected control tablet, depending on the model of the shuttle.
The same forklifts that are used to handle goods within the warehouse are also used to place the Pallet Shuttle in the desired channel. Once the Pallet Shuttle is loaded with a pallet, it moves horizontally until it arrives to the first open location, where it deposits the load.
While the Pallet Shuttle transfers and places the pallet in its location, the operator continues working. They locate another pallet, setting it in the first position of the corresponding channel. Therefore, when the shuttle returns to the front of the channel it repeats the movement uninterrupted.
The shuttle does not usually change location before it has completely filled or emptied the channel in which it is operating, or until it has finished inserting all pallets of a single SKU.
Advantages for Santa-Trans
- Enlarged storage capacity: the Santa-Trans warehouse can store 11,115 pallets with a maximum weight of 856 kg each.
- Space optimisation: channel depth in the racks achieves maximum surface area utilisation in the facility.
- Productivity boosted: the semi-automation of the warehouse offered by the Pallet Shuttle system helps to increase the volume and efficiency of workflows.
Santa-Trans logistics centre | |
---|---|
Storage capacity:: | 11,115 pallets |
Pallet size:: | 800 x 1,200 x 1,585 mm |
Maximum pallet weight:: | 856 kg |
Installation height:: | 10.5 / 8.5 m |
No. of channels:: | 195 |
Channel length:: | 50 m |
No. of Pallet Shuttles:: | 11 |
Gallery
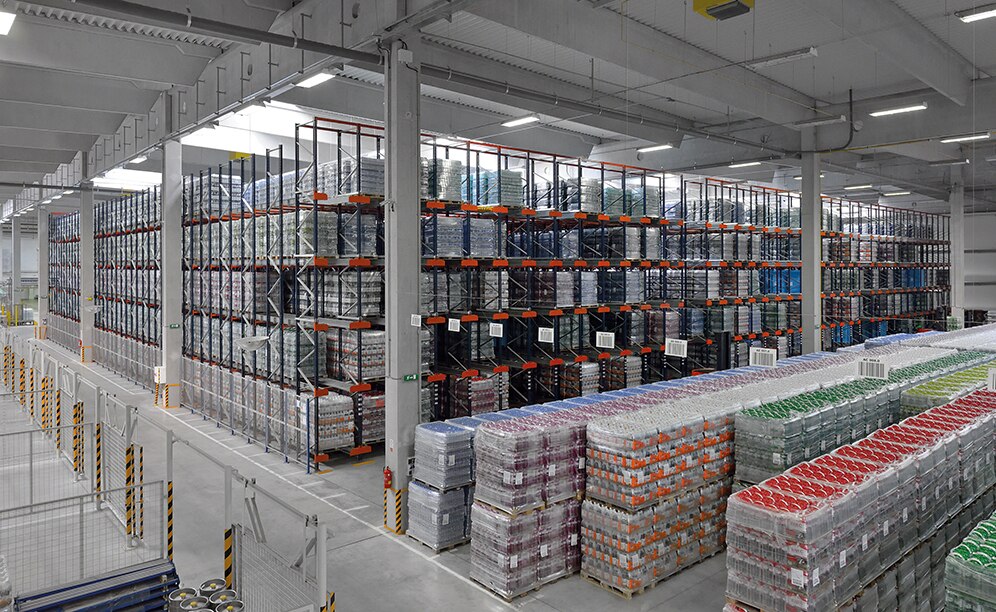
The Santa-Trans logistics centre can store 11,115 pallets
Ask an expert