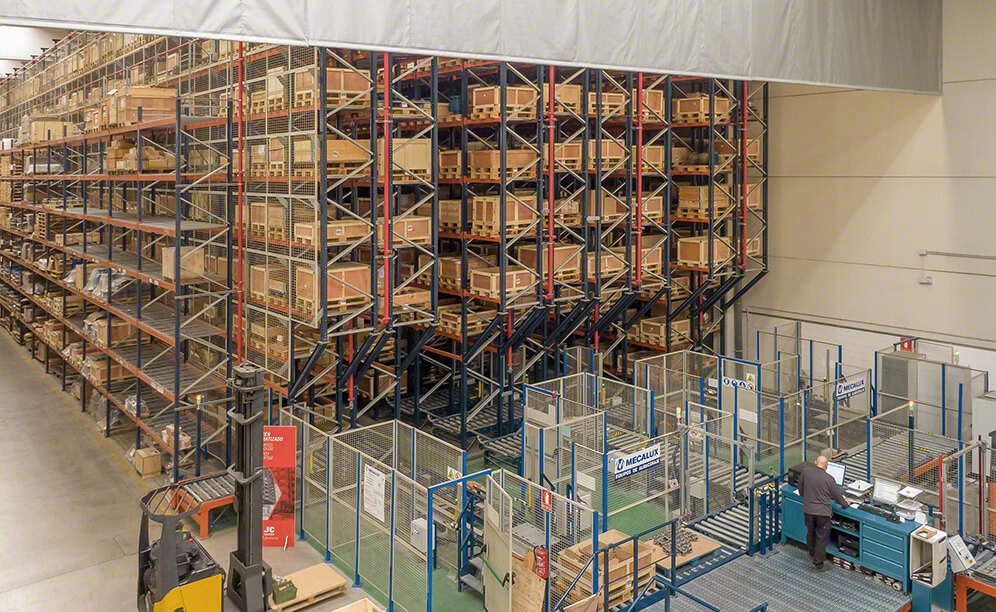
JC Valves' automated valve warehouse connected to production
JC Valves' automated warehouse is dedicated to valve making for the oil and gas, chemicals and power sectors
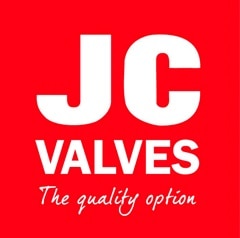
Automation has increased productivity of the installation JC Valves owns in Sant Boi (Barcelona). Recently, the company has commissioned an automated warehouse with capacity to hold 3,782 pallets right next to the production lines. Its role is to send vital raw materials to production and, at the same time, receive finished products, ready to be distributed to customers at top speeds.
Global services
Founded in Spain in 1968, JC Valves is a multinational specialised in the manufacture and sale of high-quality valves, used in any industrial sector (mainly, oil and gas, chemicals or power). It has a worldwide presence, as well as plants and offices in Brazil, Canada, China, Spain, India, Mexico, the Middle East, Russia, Singapore and South Africa.
The company offers its customers a global user experience, that ranges from technical consultation in choosing the most suitable valve, up to designing and making custom valves. As a result, JC Valves has become one of the most recognised companies globally for industrial valves.
Space optimisation
Sant Boi (just 12 kilometres from Barcelona) is the home of one of JC Valves’ largest production centres in Spain. This facility acts as the launch point for global exports to almost the entire world.
This company’s centre has a 1,700 m2 warehouse where they house raw materials and finished products. “Production and warehousing are connected together to speed up the input and output of goods. Plus, that way we always have all the materials we require in production,” points out Juan Carlos García, production manager of JC Valves.
Mecalux has installed an automated warehouse that, in the words of Juan Carlos García, “has more than met our needs, by making full use of our available space.” It is arranged in two 56 m long aisles with double-depth racking on each side that are 13 m high and offer capacity for 3,752 pallets, with each unit weighing up to 1,000 kg. Compared to double-depth ones, double-deep racks mean more storage capacity compared to the single-deep racking. All done, “without losing direct access to the pallets,” explains the production manager, “something that has provided us with more speed when it comes to managing the goods.”
Large volume of movements
Simplified warehousing operations is a feature of the warehouse: the receipt and dispatch of goods take place automatically, via a chain and roller conveyor circuit that organises pallet flows up to the corresponding aisle. Products move autonomously, avoiding mistake making due to manual management.
A stacker crane in each aisle is in charge of collecting pallets from the inbound conveyors and depositing them in the location assigned by the Easy WMS warehouse management software of Mecalux. Subsequently, it carries out the same motion, but in the reverse order when goods must flow out of the warehouse.
Automated storage tasks have yielded huge strides storage-wise for JC Valves because, in this way, “we can deal with a very high work pace easily,” says Juan Carlos García. Well-organised goods have helped provide better services and, ultimately, attend to customers’ needs faster.
Each day it receives an average of 70 pallets of raw materials from China, India, Italy and Spain. At the same time, it sends out 100 pallets with finished products to customers that JC Valves has spread around the globe.
The warehouse’s distribution is arranged to streamline order fulfilment because, as per the production manager, “we put together between 200 and 400 orders daily.” To do so, it has assembled different zones meant specifically for this operation:
- Two automatic vertical lift modules from Mecalux for small-sized products.
- A picking station at the front of the automated warehouse. Here, order picking fulfils the “product-to-person” criterion, i.e., operators remain in their picking station waiting for the stacker cranes and the conveyors that bring SKUs to them to make up each order.
- Ground floor picking area, primarily, for bulkier products.
Easy WMS: stock and picking control
JC Valves’ automated warehouse is set up to help and support the company’s logistics operations, as well as supply production with needed materials, and distribute finished products to the customers.
The installation of the Mecalux Easy WMS is a crucial step to making this possible. Its job is to coordinate all warehouse operations and guarantee the flow of goods and their movements. Easy WMS is in permanent contact with JC Valves’ ERP through communication interfaces designed specifically for this purpose.
Easy WMS needs to control all products and have detailed descriptions of their characteristics (sizes, rotation, whether raw material or finished product, etc.). “With Easy WMS, we can manage more than 4,000 different SKUs,” points out Juan Carlos García.
Easy WMS allows viewing of the warehouse map and, thus, checking of these pallets’ distribution. This process yields statistical information that helps the warehouse responsibles make any sort of decision to improve processes.
JC Valves receives items from different origins (production, suppliers, items made by other companies in the group, etc.). Each product is labelled with its own serial number so that Easy WMS can always control and carry out needed operations with the item.
Easy WMS has different location strategies configured in its programming so that products inserted into the warehouse are placed in the optimal position. These strategies are based on the stored characteristics and status of the items and the warehouse’s programmed logic.
The WMS of Mecalux also organises and presides over order fulfilment. On one hand, it is responsible for supplying needed products to the picking station at the frontal automated warehousing area and the ground-level picking zone. As such, it always has goods available for the tasks in progress and avoids service stoppages. On the other hand, it tells the operators how to prepare orders, shows them which products each order requires and where they must pick them.
Operators perform all operations with the help of radiofrequency devices. It is a highly effective system because workers can communicate with the system in real-time and receive orders and confirm when orders are completed.
Juan Carlos García - Production manager of JC Valves
“Thanks to the automated warehouse that Mecalux set up for us, we have optimised our storage space, got our hands on the storage capacity we needed for all our products and, also, sped up order picking.”.
Advantages for JC Valves
- Large capacity: the JC Valves automated warehouse has capacity for 3,752 pallets of different sizes and features a 1,700 m2 storage surface area.
- Top speeds: operations are quick, straightforward and fully-automated, thus helping workers make up to 400 orders per day.
- Warehouse connected to production: the prime objective of the automated warehouse is to supply production with raw materials throughout each day and receive finished products.
Automated warehouse of JC Valves | |
---|---|
Storage capacity: | 3,752 pallets |
Pallet size: | 800 x 1,200 mm |
Max. pallet weight: | 1,000 kg |
Racking length: | 56 m |
Racking height: | 13 m |
Levels high: | 11 |
Gallery
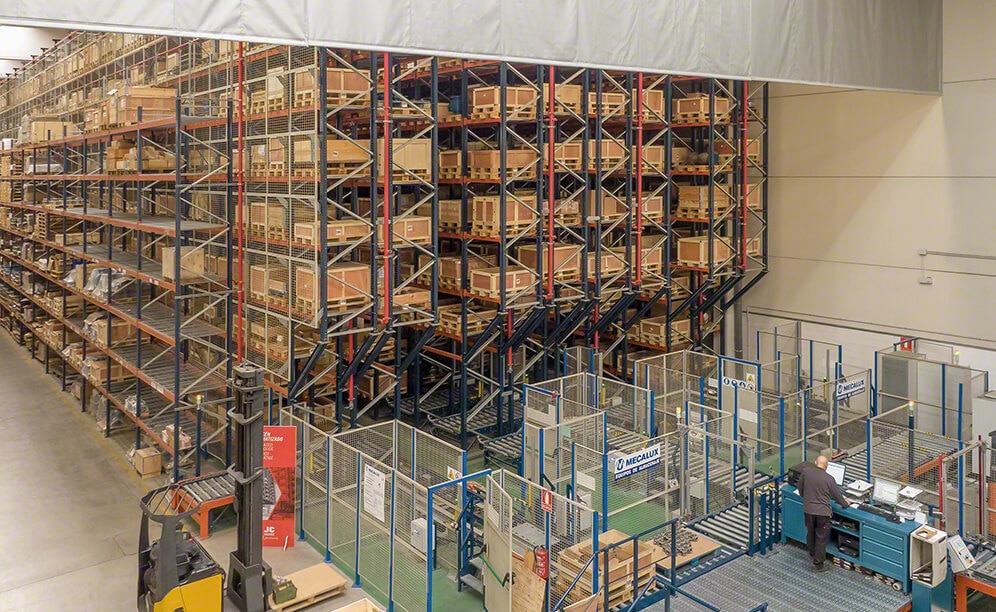
JC Valves' automated value storage in Barcelona
Ask an expert