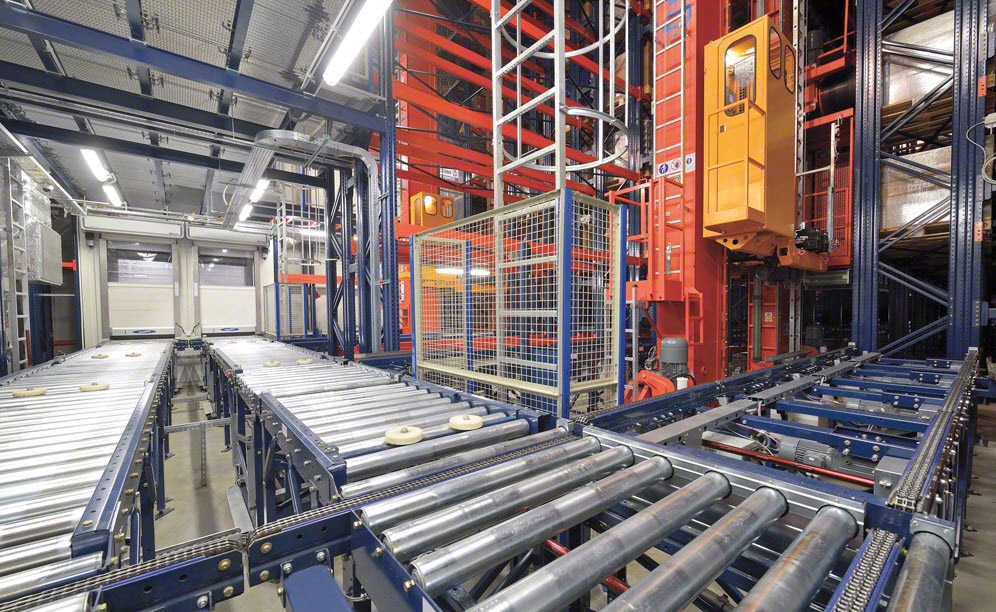
A Japanese pharmaceutical company commissions a turnkey warehouse from Mecalux in Poland
Takeda pharmaceuticals gets a 32 m high automated warehouse
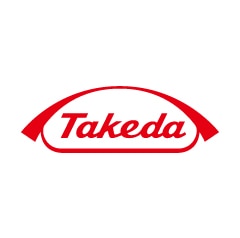
Takeda, one of the most important pharmaceutical companies in the world, has entrusted Mecalux to build a turnkey warehouse in its new Lyszkowice production plant, near the Polish city of Lowicz. The solution was to construct a temperature controlled, 32.5 m high clad-rack warehouse with a capacity to store more than 6,500 pallets. It is equipped with a cold storage system and an ‘oxygen reduction system’ for fire prevention. They were also supplied with a warehouse management system, the Mecalux Easy WMS, which is responsible for managing all the centre’s processes.
Who is Takeda?
Takeda Pharmaceutical Company Limited, with its headquarters in Osaka (Japan), is a global company specialising in the investigation of pharmaceutical products. In the mid-twentieth century, it experienced massive growth, making it a world leader in the pharmaceutical industry and the largest of its kind in Japan.
The company has a commercial presence in more than 70 countries, most significantly those in Asia, North America and Europe and emerging markets such as Latin America, Russia and China.
A clad-rack warehouse as a solution
When Takeda moved forward with the expansion of its production centre, it was very clear that the warehouse should be automated. This would allow for perfect control of stored goods, in addition to being able to achieve the maximum permissible height, given that the space available for warehouse construction was limited.
The solution proposed by Mecalux was the construction of a 32.5 m high clad-rack warehouse located next to the manufacturing facilities and the bay assigned to delivery preloading. In this type of construction, the racks themselves make up the structure of the warehouse.
The installation consists of two aisles, in which two automatic stacker cranes move independently, handling the pallets stored in double-deep racks (two pallets in depth on each level). Thanks to the optimal space utilisation, the Takeda warehouse has a storage capacity of more than 6,500 pallets in a surface area of only 950 m2.
The warehouse was equipped with a HVAC system Heating Ventilation Air Conditioning)which keeps the temperature between 16 and 24 °C and prevents the humidity level from exceeding 70%, which is something that could affect goods stored. An innovative fire protection system (inerting) has also been used, which reduces the amount of oxygen in the atmosphere to 15% to avoid fires.
The pipes of the air’s humidity and temperature control system have been installed above, targeting the aisles and placed in the free space between trusses in the facility.
For structural calculations of clad-rack warehouses the following are taken into account: its own weight; the weight of the goods stored; the wind pressure both push and suction where it is built; the weight of the snow as indicated by the regulations; thrusts by stacker cranes; and finally, the seismicity corresponding to the territory where it is located.
Due to the slenderness of the building (14.5 m wide and 32.4 m high), a highly reinforced structure was built. Also, many large sized anchorages have been placed with the aim of absorbing maximum wind pressure.
Inputs and outputs are practically unified and are constructed very simply, they are suitable for forklifts and stackers use. The entry conveyor has a checkpoint, which ensures top condition of all the pallets that are put into the automated warehouse.
The connection with the inside of the warehouse is done using a double conveyor circuit (inputs and outputs) that passes through doors with double vertical screens. The space between the two screens amounts to what is needed for a single pallet, being that the system sends alternating open and close signals, limiting temperature changes inside.
In order to avoid capacity loss, a superior platform was set up for doing secure maintenance with one access per aisle.
Turnkey warehouse
Takeda wanted all development and construction phases of the warehouse, including the supply of the software needed to properly manage all internal operations, carried out by a single company. That is why Mecalux was commissioned to run the turnkey project from beginning to end.
Stages of warehouse implementation:
- Land preparation via pilings: due to the low bearing capacity of the soil, and the large static demands, a deep foundation was made on pilings.
- Installation of a reinforced concrete foundation slab: first a reinforced top and bottom was built with steel rods, and subsequently the ground was filled with concrete.
- Finish: the foundation was finished and hardened with the objective of obtaining dust free paving.
- Rack assembly: regarding clad-rack warehouse, the racks themselves make up the actual structure.
- Assembly of warehouse cladding: in clad-rack warehouses wall panelling and ‘sandwich type’ roofs are fastened directly to the rack structure. In Takeda’s case, and having used an inerting system, it was necessary for the outside cladding to be as watertight as possible.
- Introduction of maintenance teams: conveyors and stacker cranes were assembled inside the warehouse.
- Installation of the inerting system: implementation of a fire protection system that allows you to inject nitrogen into the warehouse so that the oxygen concentration is reduced to less than 15%.
- Installing the HVAC air conditioning system: it controls the temperature that should be maintained between 16 - 24 ºC.
- Assembly of the electrical and lightning protection systems.
- Assembly of the drainage system.
- Airlock construction: the separation of the portion of the warehouse equipped with the inerting system to the adjoining building that work under normal environmental conditions.
Easy WMS
The management, synchronisation and control of the entire warehouse, including parts that interact with the maintenance equipment, work thanks to the Mecalux Easy WMS (Warehouse Management Software).
The main functions of Easy WMS are:
- Receiving and recording the pallets that come into the warehouse.
- Pallet location in the racks based on algorithms or parametrical rules.
- Management of outputs based on FIFO criteria and traceability.
- Via the Galileo software, all movements of the mechanical parts run and optimised the internal routes.
- Connection to the warehouse door control program so that it acts automatically.
- In addition, Easy WMS is in constant communication with the SAP ERP, Takeda’s main management system, exchanging orders and information that is essential to its overall management.
Avantages for Takeda
- High storage capacity in a small space: the clad-rack warehouse enables you to place 6,584, 800 x 1,200 mm sized pallets each weighing 800 kg in a surface area of 980 m2.
- Product security: pharmaceutical products stored by Takeda are protected and isolated thanks to the automatic warehouse installation. Only authorised people can access the warehouse.
- Turnkey warehouse: Mecalux was responsible for the development phases, the construction of the warehouse, the supply of storage, cooling, and fire safety systems, as well as the implementation of the WMS (Warehouse Management Software).
- Complete control: thanks to Mecalux Easy WMS, Takeda controls all the processes and operations that take place inside the warehouse, from the time the product leaves the packaging lines to its delivery.
Automated warehouse of Lowicz, Poland | |
---|---|
Warehouse capacity:: | 6,584 pallets |
Maximum weight per pallet:: | 800 kg |
No. of stacker cranes:: | 2 |
Type of stacker crane:: | twin-mast |
Fork type:: | double-deep |
Height of the warehouse:: | 32 m |
Gallery
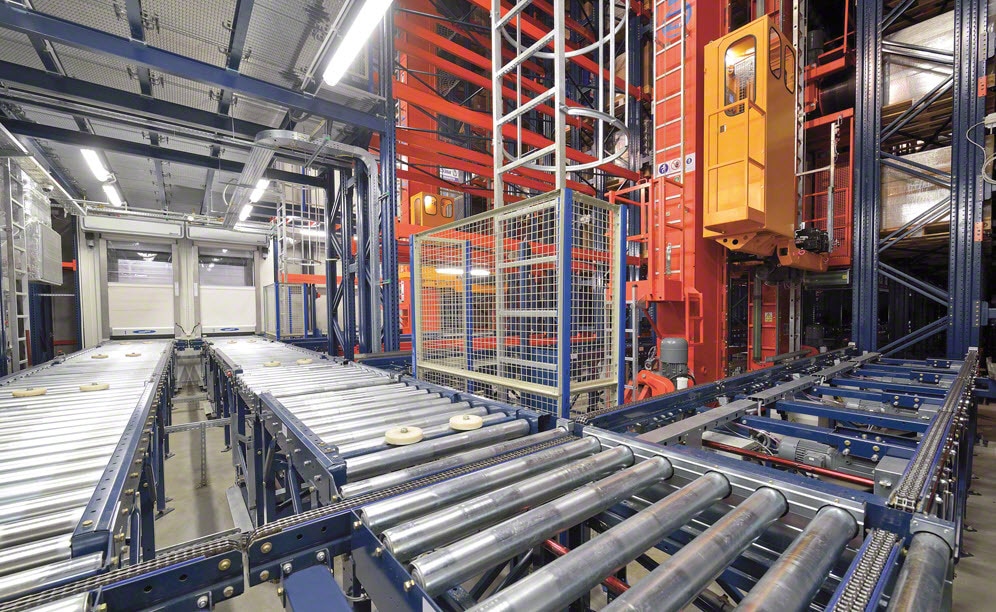
Inputs and outputs of the warehouse is done using a double conveyor circuit
Ask an expert