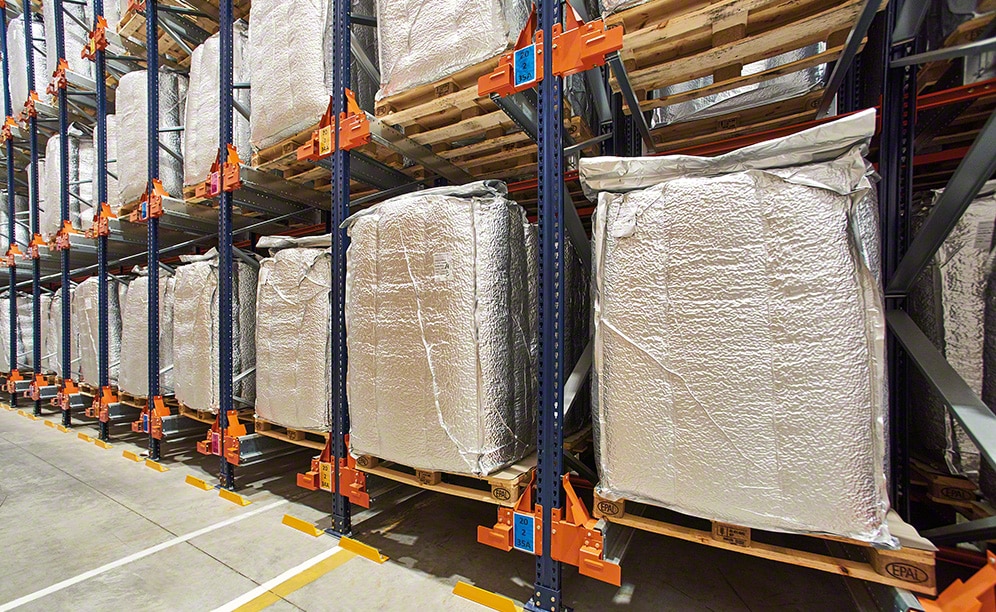
The new warehouse of the port logistics services operator Katoen Natie in Italy
Semiautomatic Pallet Shuttle in the port services warehouse of Katoen Natie in Italy
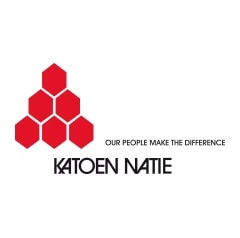
The new 3PL warehouse of Katoen Natie in Italy comprises pallet racks and the semi-automatic Pallet Shuttle system of Mecalux. These solutions max out space usage by providing a 7,765-pallet storage capacity. Racks are reinforced to protect workers and the goods from potential seismic tremors.
Multi-industry storage and transport
Founded in the Port of Antwerp (Belgium) in 1854, Katoen Natie is a logistics and harbour operator that provides 3PL services to different sectors (consumer goods, pharmaceuticals, chemicals, foodstuffs, etc.).
The business has 6,000 m2 of storage spread throughout more than 30 countries on five continents. Each of these installations is geared towards the specific needs of the customers (e.g. some are temperature controlled, others are ambient temperature, etc.).
Recently and with the guidance of Mecalux, Katoen Natie opened a new warehouse at the Rivalta Scrivia intermodal logistics platform (Northern Italy) in one of most developed, industrial regions of the country.
An earthquake-resistant warehouse
The warehouse stands 11.5 m high and is divided into four different chambers, each of which has a semi-automatic Pallet Shuttle system operated block of racks and some pallet racking. Overall, the storage capacity holds 7,765, 1,000 x 1,200 mm pallets with a 1,000 kg max weight each. The clad-rack construction, i.e. the racking, holds up their own weight loaded with the goods, the cooling equipment, as well as the wall and roof cladding.
Mecalux took the specifications laid out in the Italian NTC 2008 and European UNE-EN 16681 standards into account, to design and construct the racks. These two norms define the weight that the facade panelling and roofing of the warehouse must have, as well as the cold-generating systems.
Quakes in Italy
Europewide, Italy is the most prone to earthquakes. When the Adriatic Plate submerges beneath the Eurasian Plate (a phenomenon known as the subduction process), the latter collides with the African Plate, precipitating the tremors.
For this reason, prevention became a top priority. The buildings must comply with anti-earthquake standards that consider which measures to apply for anti-seismic structural protection. All of these norms focus on minimising the catastrophic consequences of earthquakes, to a feasible extent.
Giacomo Alberto Mongini - Project Manager at Katoen Natie
“Design and implementation times for this project were very swift. Mecalux has shown exemplary service by delivering the Pallet Shuttle system to specifications and on time. All our expectations were met, in terms of time used to supply and put up the racks.”
Vacuum packing guaranteed
The new Katoen Natie warehouse is set aside to house the raw materials of one of its main customers, a leading Italian company in the sweets industry. The company uses big-bags to store bulk products, hazelnuts in this case. These sacks are set on pallets, which facilitates their handling and storage in the racks. Before flowing into the warehouse, the bags cross through a vacuum-sealing process to preserve the natural freshness of the dried fruits and nuts during the months they might remain stored.
Katoen Natie’s customer places critical importance on vacuum-packing to ensure the top quality of its products. “Keeping vacuum-packed items air-tight is a priority. That is why the stored material needs periodic checks,” pointed out Giacomo Alberto Mongini, project manager at Katoen Natie. Mecalux kept this in mind when it designed the storage systems and supplied a solution that would ease the control of goods.
The uppermost racking level is shorter than the others, meaning pallets cannot be deposited there since they do not fit. Thus, only a Pallet Shuttle runs through this level. The shuttle has a built-in camera, whose transmitted images are viewed by operators via a tablet; who, thus, inspect the condition of the bags and verify that their vacuum-packing is still intact.
Keys to operating a warehouse
As per the company’s project manager, “The Pallet Shuttle system has substantially cut times for handling merchandise. Plus, it has reduced risks that could cause accidents, by keeping reach trucks from having to enter into the storage lanes.”
In fact, the storage system runs in a very straightforward way, and inputs and outputs are swift. Operators place the Pallet Shuttle into the corresponding channel, deposit pallets into the rack’s first position and the shuttle transfers these to the first open location. The reverse operation is carried out to extract the merchandise.
Katoen Natie reaps enormous benefits from this feature, since the product has a seasonal inflow (with very high peaks between January and April), even though outputs are constant throughout the whole year (pallets move to manufacturing every day, located just a few kilometres from the warehouse). Ultimately, the Pallet Shuttle system made hitting top speeds a reality.
Additionally, for this warehouse, all available space was thoroughly used to “boost the storage capacity in the same space,” explained Mongini.
Advantages for Katoen Natie
- Speedy compact system: among dense storage solutions, the Pallet Shuttle is the most flexible for smoother insertion and removal of pallets in channels, with minimal operator intervention.
- Merchandise managed: the products require stringent control to prevent vacuum-packing from bursting. The Pallet Shuttle system includes a camera to check the condition of the pallets without removing them from their locations.
- Anti-tremor protection: the warehouse is specially protected against environmental constraints found in a zone with such a high risk of seismic activity.
Pallet Shuttle system | |
---|---|
Storage capacity: | 6,850 pallets |
Pallet size: | 1,000 x 1,200 mm |
Max. pallet weight: | 1,000 kg, |
No. of channels: | 780 |
Racking height: | 11.5 m |
Racking length: | 62 m |
Channel depth: | 13 m |
Gallery
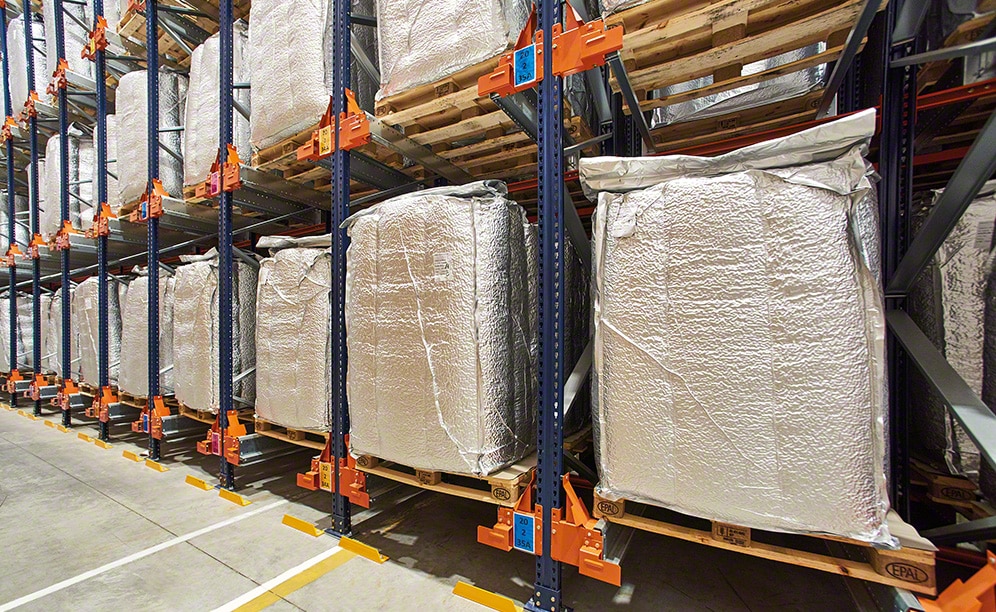
The port services warehouse of Katoen Natie in Italy is a clad-rack building
Ask an expert