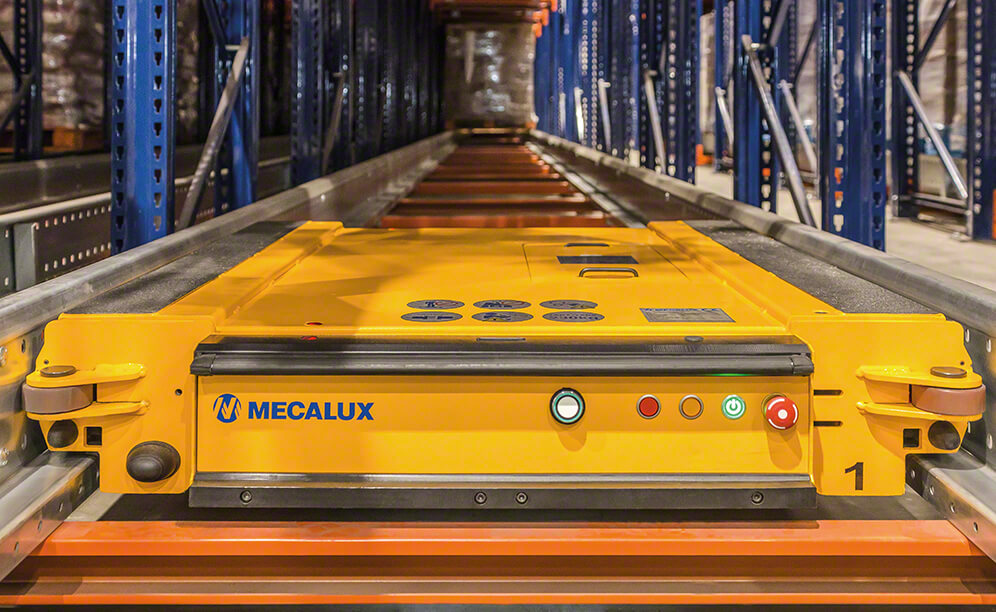
Compact storage systems at Selmi's new warehouse in Brazil
Selmi has renovated its warehouse with the semi-automated Pallet Shuttle system and drive-in racking
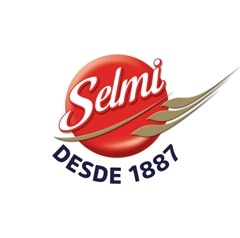
The Brazilian food company Selmi has renovated its warehouse in Rolândia (State of Paraná) by installing three Mecalux storage solutions: pallet racks, drive-in racks and racks with the Pallet Shuttle system. Combining these systems provides a storage capacity for 3,263 pallets. It helps classify the goods according to their demand and expiry date, which simplifies the operators’ work and speeds up the housing and distribution of 1,400 pallets per day.
Italy to Brazil
Selmi is one of the largest food companies in Brazil. It was started in 1887 under the guidance of Adolpho Selmi, when he emigrated from Italy and disembarked at the Port of Santos (in the State of São Paulo) hoping to spread the culinary tradition of his homeland.
Today, the company has two factories in Brazil: one in the town of Sumaré and another in Rolândia. It also owns and operates ten distribution centres in the cities of Rio de Janeiro, Curitiba, Itajaí, Brasilia, Belo Horizonte, Campo Grande and Canoas, with over 17,000 m2 of storage space altogether.
Fresh logistics
Logistics is one of Selmi’s main activities. Thanks to a solid supply chain organisation, Selmi delivers orders up to 72 hours from when customers request them.
To achieve this, it has reorganised the distribution of its 5,175 m2 warehouse based in the town of Rolândia. “It is located in a strategic region, very close to our customers so we can dispatch orders fast. However, improving product management was at top of our list and wanted to make our space count,” explained Márcio Aparecido Santiago de Oliveira, general manager at Selmi.
The company’s priority was to secure as much storage capacity as possible, while still efficiently managing the many different SKUs within its product catalogue. The company sought out the Mecalux’s input because, in the words of the general manager, “this is a multinational with a long-established track record and expertise in the logistics sector.”
Mecalux has equipped the Selmi warehouse with three different storage systems: pallet racks, drive-in racks and racks with the Pallet Shuttle system. “The installation went quickly. It met the agreed deadlines and we continued doing business as usual without interruptions in our customer service,” Santiago de Oliveira declared.
Each day, the warehouse receives an average of 700 pallets with finished products directly from manufacturing. It also dispatches another 700 for quick deliveries to the company’s customers (mostly in Brazil).
Having different storage solutions in the same space has the advantage that operators can sort goods according to their characteristics and demand level. “We have achieved a swift flow of goods, can store them all in perfect condition and no mistakes occur,” Selmi’s manager said.
Pallet racks
They are 9 m high and have a storage capacity for 336 pallets. A unique feature of these racks is that they give direct access to the products, which speeds up the storage and order fulfilment work.
Versatility in pallet racks also means that different sized goods can be stored in the seven storage levels that it has at its disposal. These racks store pallets of a range of items, such as spaghetti, macaroni, instant noodles and biscuits.
Drive-in pallet racking
They comprise a set of lanes with pallet support rails at each level. There is room for a total of 1,127 pallets filled with finished products.
Operators, pushing reach trucks, enter the inner lanes with the load raised above the level where it is going to be deposited. On the floor, guide rails make it easier for forklifts to be centred and move safely inside lanes, minimising accidental damage to the racking.
High-density racks and the Pallet Shuttle system
Mecalux has fitted out two blocks of 11.5-metre high, six-level, 28-metre-long compact racks with space for 25 pallets depth-wise. In total, up to 1,800 pallets can be stored, with a 1,000 kg maximum unit weight.
Advantages of the Pallet Shuttle system
“The Pallet Shuttle has optimised the capacity of the warehouse and, at the same time, has sped up the entry and exit of goods,” Oliveira said. This high-density system makes use of all the available space. It offers greater storage capacity and features an electric shuttle that inserts and extracts pallets from their locations with total autonomy.
It operates quickly, simply and requires minimal movements: the operators place the motorised shuttle into the channel, they deposit the pallets into the first position of the racks, and the Pallet Shuttle transfers them directly to the first free location autonomously.
By eliminating the need for forklifts inside storage lanes, Selmi has reduced maintenance costs: fewer handling equipment means fewer blows to the rack structure, for example.
“Since we carry food products—meaning expiry sensitive products—, we work according to FIFO criterion (first in, first out),” the company manager said. The pallets are funnelled into a storage lane and unloaded at the opposite end of the rack.
Márcio Aparecido Santiago de Oliveira - General Manager at Selmi
“We have reaped the benefits of the Mecalux Pallet Shuttle system, especially the sound inventory management. I can’t tell you just how satisfied we are with the storage solutions installed by Mecalux. We already plan to implement more racks in the rest of the warehouse.”
Efficient food product management
With three different storage systems in place, the company can better organise its goods. The warehouse’s distribution has an impact on the operators’ work when it comes to locating the items requested by customers. Consequently, it also affects the delivery timeliness.
The racks make use of the warehousing area, so Selmi gains the biggest possible storage capacity. The company has also implemented the Pallet Shuttle system, a solution that adds speed to the pallet inputs and outputs.
In short, all three Mecalux solutions have been completely geared to Selmi’s unique way of doing business, with its different product sizes, characteristics and rotations.
Advantages for Selmi
- Warehouse organisation: each item is placed on the most suitable racks taking into account its characteristics and level of demand, which speeds up the preparation of orders.
- Storage capacity: the three Mecalux storage systems take advantage of the available space and offer a total storage capacity for 3,263 pallets.
- Agile operation: the Pallet Shuttle system is equipped with a motor-powered shuttle that inserts and extracts the goods from their locations without any additional intervention, i.e. autonomously, making storage tasks much quicker.
Selmi warehouse: Semi-automatic Pallet Shuttle | |
---|---|
Storage capacity: | 1,800 pallets |
Pallet size: | 1,000 x 1,200 mm |
Max. pallet weight: | 1,000 kg |
Racking height: | 11,5 m |
Gallery
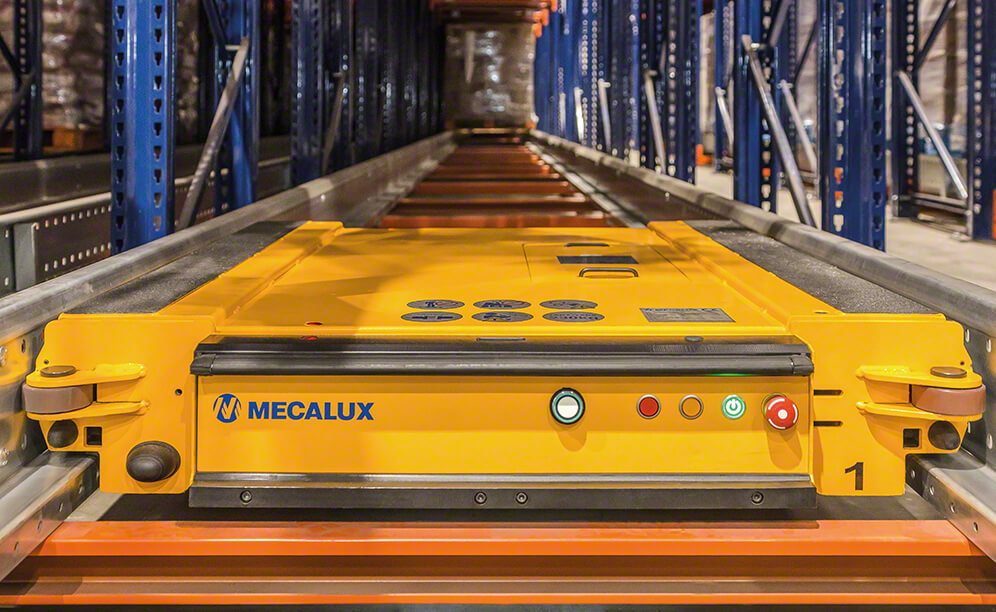
Storage of macaroni and spaghetti at the Selmi warehouse
Ask an expert